One of the first measurable factors a vibration testing laboratory identifies is the resonant frequency of the device under test (DUT). Resonance is a typical source of unwanted vibration and material fatigue that leads to failure.
Resonance occurs when an excitation frequency equals the DUT’s natural frequency, amplifying the vibration’s amplitude. It appears as a peak in amplitude on a graph. When unaddressed, resonance leads to failure.
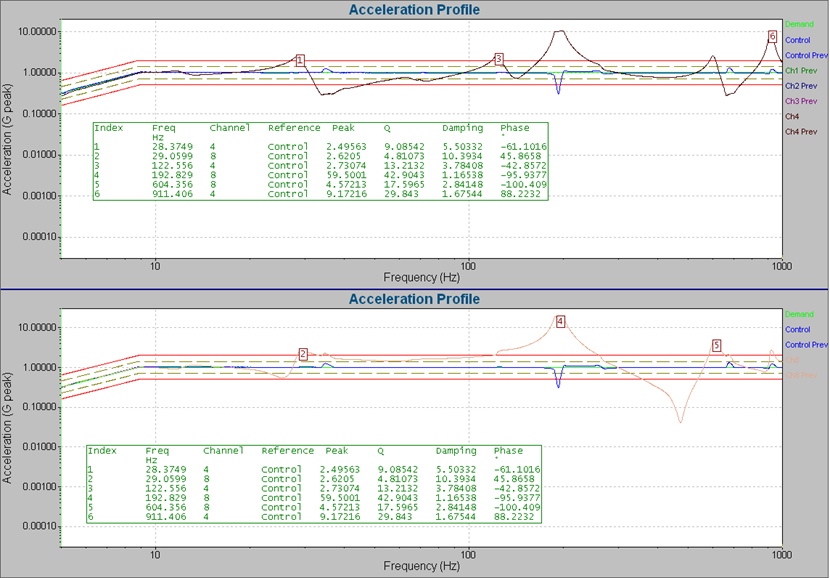
Resonance annotation in VibrationVIEW Sine software.
Two test types that identify resonance are sine vibration testing and modal testing. Single input, multiple output (SIMO) modal testing is the closest method to sine vibration testing but requires a different test system. This article explains the differences in these test types when choosing between them.
Excitation Methods
Sine Vibration Testing
Sine vibration testing uses a shaker to apply a single-frequency sine wave to the DUT. A typical test system can measure the response at critical points in acceleration, velocity, or displacement.
Most significantly, sine tests output one frequency at a time. Tests like sine sweeps output a range of frequencies but individually and incrementally. The sine wave runs as a constant signal, uninterrupted throughout each test level, unless in the case of an abort.
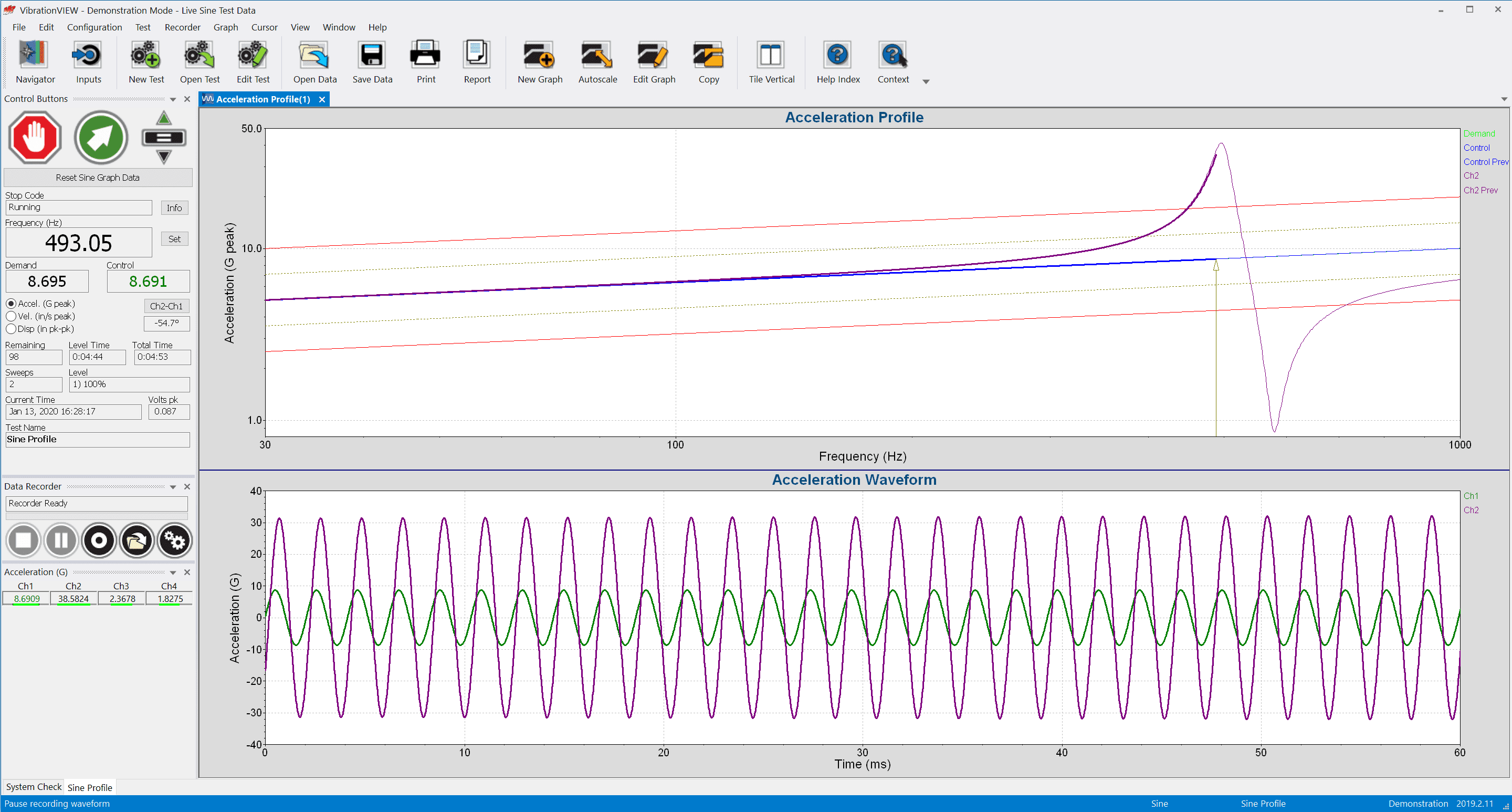
Sine sweep profile in the VibrationVIEW software.
Using a control sensor, the test engineer can control the excitation on the shaker table, avoiding excessive damage. Vibration control is ideal for engineers working with expensive or one-off DUTs or determining resonance without fatiguing the DUT.
SIMO Modal Testing
SIMO modal testing excites the DUT at a single point at a time, often with an impact hammer, although shakers can also perform modal testing. An impact hammer is a measurement tool that produces transient excitation upon impact. A shaker offers more control over the excitation, but it is typically a short-duration, pseudo-random signal.
The DUT’s response to modal excitation is measured at multiple points to identify mode shapes that help describe the structure’s response. A modal setup can require many sensors and a system capable of high-channel-count data acquisition, depending on the size of the DUT.
Purpose
Sine: Resonance Search and Characterizing Initial Designs
Sine testing outputs a constant sine wave to excite any potential resonant frequencies. After resonance is identified, a sine dwell may be run to determine how long the DUT can resonate before fatigue/failure occurs. With sine shaker test data, engineers determine if the design must be adjusted to avoid resonance.
SIMO Modal: Structural Dynamics and Validating Designs
Modal testing is run with the intention of performing modal analysis. In addition to natural frequencies, modal test collects data like mode shapes and damping ratios to model the DUT’s dynamic behavior. Modal analysis provides more options than sine testing for optimizing a design. Engineers can model predicted behavior, find deflection shapes, and simulate behavior following changes to the design.
Differences
Whether a laboratory selects a sine vibration test or modal test for a resonance search depends on available equipment/budget, its design approval process, and, possibly, the stage of design development.
Sine vibration testing is common during procedures like design failure mode and effect analysis (DFMEA), which occurs early in the product development cycle. Sine testing is a straightforward method of identifying resonant frequencies and is typically easy to set up.
A closed-loop vibration test also offers the benefit of controlling excitation at specific frequencies. Generally, sine testing offers higher frequency resolution than modal testing because it can sweep through frequencies more precisely.
Typically, laboratories perform sine tests on individual components and often, but not always, on smaller DUTs. If your goal is to identify the resonant frequencies of a component’s early design, vibration testing should be a fitting application. That said, a laboratory may perform sine vibration testing early in the product development cycle and modal testing later, as modal analysis can function as a design validation method.
Modal testing is often reserved for large test items or complete structures. It may be selected for test items that cannot fit on a vibration shaker or complex structures that require modeling for comprehensive analysis. Modal analysis provides more details about the test item’s behavior than sine testing and requires a more involved setup.