Software
What are the PC specifications for the software?
Download the VibrationVIEW PC Specifications document.
Download the ObserVIEW PC Specifications document.
Which Vibration Research hardware and software are compatible?
The user can run any of the three Vibration Research software applications (VibrationVIEW, ObserVIEW, and VR Mobile) on all VR hardware. Each software package offers different capabilities when paired with the hardware.
What is VR Mobile?
VR Mobile is embedded software that runs on Vibration Research hardware. The user can connect to VR Mobile and interact with the software on a smartphone or tablet using a WiFi connection.
Can I test your products before purchasing?
Put us to the test! Our software is free to download, and you can activate a free online trial of our paid features. Simply click to activate! We also offer free 30-day demos of our hardware so you can experience how well our hardware and software are integrated.
VibrationVIEW
Where can I find which packages and software version I have?
Select Help > About VibrationVIEW to view the version of your software and the installed packages. The version number is also printed on the VibrationVIEW CD label.
The packages for VibrationVIEW can be viewed on the control software page.
Can I purchase additional software modules after my initial system purchase?
Yes, you can contact a member of the Vibration Research sales team or your sales representative to enable additional software modules. Delivery is fast and easy. You will receive a link to download a key update file; install the key update file and the new software module will be enabled.
What is the latest version of VibrationVIEW?
- View the latest updates for the VR9500/VR10500 units here
- VibrationVIEW 2016.2 for the VR8500 unit
- 3.1.7 for the VR7500 unit
If you purchased your vibration control system from Vibration Research in the last year or have a current Upgrades & Support Agreement, then you are entitled to free software updates. If your system is more than a year old, call Vibration Research at 616.669.3028 or email us.
What is Quick Test?
The Quick Test option serves as the default for Sine, Random, and Shock tests. It is a quick option for defining tests and requires the entry of just a few simple parameters. Selecting the Advanced button on the bottom left of the dialog box directs the user to VibrationVIEW’s standard multi-tab dialog box.
The Quick Test option can be removed as the default if it is not preferred. To set the Advanced test option as the default for the Sine, Random, and Shock modes, select Configuration > Parameters. On the left, point to Global Parameters and deselect “Define new tests as Quick Tests.” Select OK.
VibrationVIEW says my key has expired. What should I do?
If your control computer is connected to the internet:
- Select Help > Check for Key Update in the VibrationVIEW menu.
- Upgrade to the most current VibrationVIEW software version.
- Verify that your controller invoice has been paid.
- Verify that your master controller is set to Channels 1 to 4 in Configuration > Hardware.
- If you are still experiencing issues, please contact Vibration Research at support@vibrationresearch.com or call 616.669.3028.
Windows Defender Firewall is Blocking VibrationVIEW. What should I do?
The user may encounter a situation where VibrationVIEW cannot communicate with the controller. The underlying reason may be hard to pinpoint: a new VibrationVIEW version may have been installed or Windows Updates may have introduced a change. Most often, however, the issue is due to the Windows Defender Firewall blocking VibrationVIEW, even if the Firewall is off.
Follow these steps to ensure VibrationVIEW is allowed through the Windows Defender Firewall.
- Navigate to the Windows Start button on the bottom left of your screen.
- In the Search Bar, type “Allow an app through Windows Firewall.”
- Select the Allow an app through Windows Firewall option.
- Select the Change Settings button.
- Make sure all the VibrationVIEW entries on the list are selected for Domain, Private, and Public networks.
- After selecting all the boxes, select OK.
How do I generate an automatic Random Import profile?
Select the Import tab on the Random Test Settings dialog box.
From there, you can automatically generate a spectrum profile from input data. The input can be a set of frequency/amplitude breakpoints or a time/acceleration history stored in a text file.
To input data from a file, perform the following procedure:
- Select the input method from the drop-down list.
- Select the input file button and choose a file. The software will scan the file, and the dialog box will update to reflect the contents of the file.
- Set the sampling rate, header lines, and column number for the acceleration data, and the acceleration units used in the file.
- Select the spectrum generation method. The import procedure will divide the file into 1,024 sample blocks, compute the spectrum for each block, and then combine the blocks according to the selected method. Average will average all the spectra using a uniform average. Peak hold will extract the peak values over all the blocks at each frequency.
- Select the Create Table button to process the file and create the frequency/amplitude breakpoint table from the input file.
ObserVIEW
Where can I find which features and version number I have?
Select File > Settings > License to view the version of your software and the activated features. The version number is also printed on the ObserVIEW CD label.
The licenses for ObserVIEW are Basic, Advanced, Order Analysis, FDS, SRS, and Modal Testing. A license key is optional. Contact Sales to enable additional features.
How many PCs can I activate with one ObserVIEW license key?
Per the EULA, the software may be installed on any number of PCs provided that it is used on one PC at a time. A reasonable number of PCs registered with the same key is allowed.
If the PC activation limit is exceeded, the license activation will fail. VR support must be contacted to resolve the activation issue. Additional activation may be granted provided that the user adheres to the license terms.
Is there a way to deactivate a license?
Contact VR support to deactivate a PC license.
Can ObserVIEW receive a license from my hardware box?
Yes, the user can activate ObserVIEW by connecting to a VR I/O unit licensed for use with ObserVIEW (ObserVR1000, VR9500, or VR10500).
I don’t own VR hardware. Can I open my recordings in ObserVIEW?
Yes, the software can import .txt, .csv, .uff, .wav, and .mat files in addition to Vibration Research recording files (.vfw).
Can ObserVIEW fulfill IEC 61672 requirements for sound level measurement and overall RMS?
Yes, our octave plot makes it easy to analyze sound data, measure the dB levels, and find the overall RMS for each channel. The results can be exported as a report with images and data sets with one click.
Reports
How do I automatically generate a report when my test completes?
To automatically generate a report in VibrationVIEW, follow these steps:
- Select Edit Test to access the test settings. Select the Schedule tab.
- If you are in “Simple” test mode, select the Advanced button to navigate to the Schedule tab.
- Select Insert to add a row to the end of your test schedule.
- Navigate to the leftmost drop-down list in the new row and select Save Report.
- In the same row, select the Browse button and select the report template that the program should use.
- Select the Data tab. Below “Data storage directory” select Browse. Select the directory where the program should store the automatic report.
- Below “Save data to disk/Save waterfall slice” select your choice(s) of three automatic report options.
Note: Below “Graph annotation lines,” you can enter information such as test sample number, test technician, shaker serial number, etc. to be included in the report.
How do I make a custom report template?
To make a custom report template in Microsoft Word, follow these steps:
- Navigate to the template directory. The default is C:VibrationVIEWTemplates. Select the folder of the relevant test mode.
- Right-click on the template you would like to modify and select Open.
- A template in Rich Text Format will appear. Edit the parameters as you would like them to appear on your reports. For details on these parameters, please see the software manual or select View > Report Parameters in the VibrationVIEW software. The parameters in the Help file can be copied and pasted into your template. You can also paste your company logo into this template.
Note: The program uses separate templates for each test mode.
For a more detailed explanation of forms and reports, watch our webinar on the topic.
Hardware
Where can I register my hardware, and why should I do so?
You can register your VR hardware online.
VR9500/VR10500
You will access a free, 1-year upgrades & support agreement (U&SA) by registering your VR9500/VR10500. Renewals are available on an annual basis, and continuous coverage with no lapses ensures a lifetime guarantee on your hardware.
ObserVR1000
You will activate the 1-year hardware warranty on the ObserVR1000 by registering your device.
How many channels do the Vibration Research systems support?
- VR8500 supports up to 32 channels.
- VR9500 supports up to 128 channels.
- VR10500 supports up to 512 channels.
- ObserVR1000 supports up to 128 channels.
What is your hardware warranty?
VR warrants its hardware to be free of defects in material and craftsmanship. The warranty covers hardware failure under normal conditions. It does not cover damage due to wear and tear, neglect, misuse, or failure to follow instructions relating to the hardware’s use. Please contact Vibration Research or your sales representative for more information about our warranty.
VR9500/VR10500
The VR9500 and VR10500 hardware includes a three-year hardware warranty that can be extended to a lifetime warranty by continual renewal of an upgrades & support agreement with no lapse.
ObserVR1000
The ObserVR1000 hardware includes a one-year hardware warranty.
How can I get a demonstration of a Vibration Research hardware unit?
Call Vibration Research Corporation at (616) 669-3028, email us at vrsales@vibrationresearch.com, or talk to one of our representatives.
What is the difference between the VR8500 and the VR9500?
Specifications
VR8500 | VR9500 | |
Hardware Warranty |
No |
Lifetime |
Processor |
RISC Processor |
Dual High-Speed RISC Processor |
Lines of resolution |
13,000 |
26,000 |
Max control frequency for Sine |
0.1 to 20,000Hz |
0.1 to 50,000Hz |
Max control frequency for Random |
0.5 to 20,000Hz |
0.5 to 50,000Hz |
Sample frequency |
Up to 52,000Hz |
Up to 200,000Hz |
Narrow spectral bands with Random-on-Random |
Up to 12 |
Up to 32 |
True floating-point sine tones with Sine-on-Random |
Up to 12 |
Up to 32 |
Sine includes COLA and notching |
No |
Yes |
Random includes notching |
No |
Yes |
Dynamic range |
>120dB |
>130dB |
Light indicators on hardware show sensor connection |
No |
Yes |
Self calibration |
No |
Yes |
Ethernet connection speed |
100Kps |
1000 Kps (gigabit) |
Noise floor |
Not applicable |
<70nV/vHz |
Clock synchronization |
No |
Yes |
Multi-axis testing ability |
Yes |
Yes |
I have a VR8500. Why should I upgrade my hardware?
Upgrade to the VR9500/VR10500
Discover the new and exciting features of our latest controllers and read more on why you should upgrade: Vibration Controller Systems.
How can I view a controller's dynamic range?
The importance of a vibration controller’s dynamic range is often misunderstood. A controller may specify the input or output dynamic range or the overall range.
Rather than referencing the specifications, you can run a test with the controller to view the total system dynamic range. To run the test, create a Random profile with a section of the profile reduced to nothing. You can determine the random dynamic range by observing the actual level of the profile.
The Chinese government uses test specification JJG 529-88 to specify a system’s dynamic range. The engineer can run the test on a shaker system or on the controller “looped on itself.” The test has the following breakpoints:
20 Hz | -40 dB |
80 Hz | 0 dB |
300 Hz | 0 dB |
350 Hz | -40 dB |
350 Hz – 500 Hz | no energy |
500 Hz | -40 dB |
600 Hz | -20 dB |
650 Hz | -20 dB |
700 Hz | 0 dB |
750 Hz | -20 dB |
800 Hz | -20 dB |
1000 Hz | 0 dB |
1500 Hz | 0 dB |
2000 Hz | -20 dB |
The VR9500 demonstrated a dynamic range of 90+dB with JJG 529-88. Many controllers that claim 80dB of dynamic range show only 50dB or 60dB with these specifications. Lack of adequate dynamic range may cause system problems when controlling a fixture with a large resonance.
The figure below displays a more detailed explanation of the dynamic range.
For a more detailed explanation, please see the paper “Examining the Dynamic Range of Your Controller.”
Is my controller working properly?
Sometimes, a vibration testing system generates errors or does not operate, and there is no clear cause. It could be a loose connection, frayed cables, issues with the amplifier, a malfunctioning shaker, or, in rare cases, a problem with the controller. Loopback Diagnostics is a straightforward way to determine if your controller is working properly.
Loopback Diagnostics is a VibrationVIEW tool that allows the user to verify the functionality of a VR9500/VR10500 controller. It internally connects the Drive or COLA to the input channels (usually during a System Check test), eliminating the need for BNC cables or running a shaker.
CAUTION: The Drive and COLA outputs remain active in Loopback mode. By looping the Drive back to the control channels, you are running the controller open-loop (the control channel is disconnected from any accelerometer connected to the input channels). Make sure to disable your shaker or disconnect the drive cable to prevent shaker movement.
CAUTION: Channels connected in Loopback mode must be disconnected from any accelerometers or input sensors. Any channel limits defined in the System Check test profile will be enforced on the Loopback signal, not the actual input signal.
For detailed instructions on setting up and running Loopback Diagnostics, please see the following video:
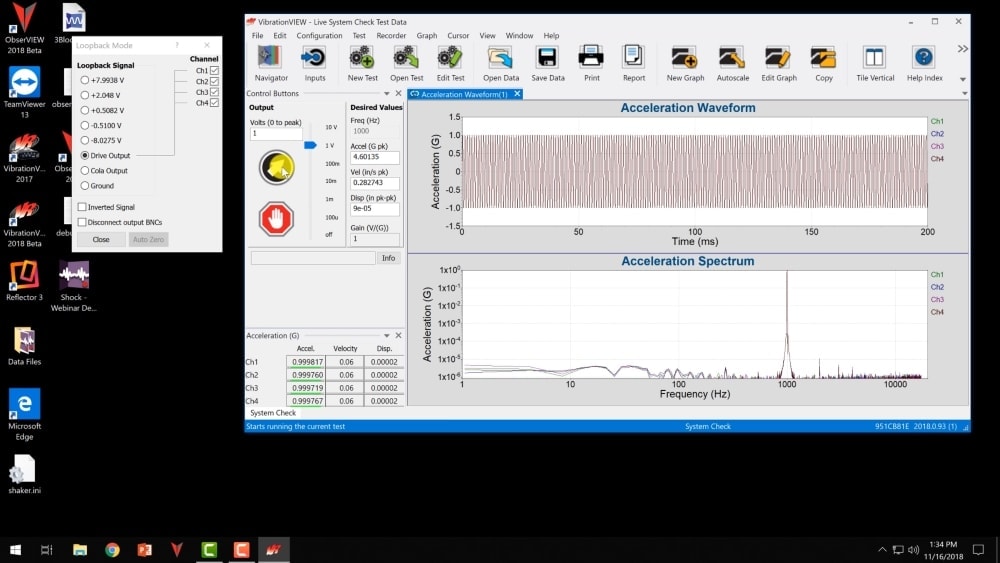
If the input channels are displaying accurate voltages, then the problem is in one of the other components and not the VR9500/VR10500.
Manuals
Where can I get an electronic copy of the manuals?
There are several manuals for Vibration Research hardware and software:
-
- VibrationVIEW operation manual
- ObserVIEW operation manual
- VibrationVIEW Quick Start Guide
- ObserVR1000 Quick Start Guide
- Hardware manuals (VR9500, VR10500, and ObserVR1000)
All manuals are located on the software CD in the Manuals directory in a Word (.doc) or PDF format. The Word version requires Microsoft Word or the MS Word Viewer. The PDF version requires Adobe Acrobat Reader.
The manuals relevant to VibrationVIEW/ObserVIEW can be accessed in the Help file of the software.
The manuals can also be manually downloaded.
Emergency Stop Button
Why is the emergency stop button an important safety feature?
The emergency stop (e-stop) button provides further safety measures for lab personnel, testing equipment, and products under test. It gives lab personnel a quick option to stop a test without putting a transient shock into the device under test.
How do I install an emergency stop button?
If you selected the optional e-stop button for your controller:
- Plug the Phoenix connector into the back of the I/O unit.
- In VibrationVIEW, select Configuration > Remote Inputs.
- Point to the eighth drop-down box and select “Emergency Stop Button.” Select the OK button.
Watch this quick tip video for a walkthrough of the software.
Calibration
How often should I calibrate my VR hardware?
We strongly recommend an annual calibration. The system arrives factory calibrated, so you do not need to calibrate it again until the due date on the calibration certificate.
What are my options for calibration?
There are three calibration options for the VR hardware:
- Send the hardware to Vibration Research for calibration.
- Calibrate the hardware yourself with VR Software.
- Perform the calibration yourself.
Please see our calibration page to read more about these options.
My accelerometers require a recalibration: what do you suggest?
VR’s accelerometer calibration performs automatic and accurate calibration and verification of IEPE accelerometers and charge-mode piezoelectric accelerometers in your lab.
Otherwise, we suggest that you send your accelerometers directly to the manufacturer for recalibration. If you purchased your accelerometer directly from VR and are not sure who the manufacturer is, contact us for more information.
I am experiencing trouble with calibration verification in my lab. What could be the issue?
Performing calibration verification in your lab can save time and money, but sometimes the process stops and it is not clear why.
Problems usually arise at one of two steps:
- If the Next > button is unavailable after selecting the device and configuration, then the analog connections (output to channel inputs) are not functioning and the verification process cannot move forward (see image below).
Check the cables and the connectors, as some components may be worn or frayed and have stopped functioning.
- VibrationVIEW populates the Certificate Entry form, including the digital multimeter (DMM) type. If the DMM is not connected properly, or if it is an unsupported DMM, then VibrationVIEW will not populate the form with the DMM information (see image below). The procedure may continue but will stop intermittently or fail because the appropriate connection between the DMM and the PC has not been established.
The most common DMM connection problem is due to a USB to serial adapter that isn’t fast enough to keep up with VibrationVIEW transmission speeds. Vibration Research recommends a B+B Smartworx USB to serial adapter (part number: 232USB9M). If you have a PC with a serial port, you can connect to the DMM directly with a null-modem cable instead.
If you are still experiencing trouble with the calibration verification procedure, please contact us.
Shakers
What shakers can I control with my Vibration Research controller?
Vibration Research systems can control all electrodynamic and servo-hydraulic shakers.
How do I determine the correct shaker size?
The industry uses the equation Force = Mass x Acceleration as the basis for sizing shakers and determining if a shaker can perform a shock or vibration test. All shakers have a force rating that determines what combination of mass and acceleration the shaker can achieve.
To perform a quick F=MA calculation, visit the calculator page.
What is total harmonic distortion?
Total harmonic distortion (THD) is the summation of the amplitudes of various harmonics when a pure sine tone is inputted into a system. THD not only measures the quality of a sine wave but can determine how well a system is replicating the signal from the controller. Small values indicate the system is performing as requested. In the physical test environment, a high value suggests a weakness or malfunction of the shaker system.
THD can be used to measure the accuracy of a vibration system and help to track system changes over time. You can buy harmonic distortion analyzers to perform the measurement for you or use equipment you already have in your laboratory: a vibration controller/analyzer.
How can I measure the THD of my shaker with my vibration controller?
You can measure THD by exciting your system with a sine wave, reading the g2/Hz displayed by the system, and noting the difference in dB between the fundamental frequency and higher-order harmonics. The harmonics occur at 2x, 3x, 4x, etc. of the fundamental frequency. As most controllers read directly in g2/Hz, a change in 10x g2/Hz is a 10dB change. For example, 0.1 g2/Hz to 0.01 g2/Hz represents a 10dB change.
Remember: dB = 20 log (A/B). Thus, a 10% distortion (0.1 ratio) will appear as -20dB.
-20dB = 20 log (0.1)
The following is an example of harmonic distortion from a sine wave generator. The generator was set to 100Hz. The third harmonic is the highest spike at 40dB (4 major divisions) down from the 100Hz fundamental. This test reports the third harmonic distortion at 1%, which matches the specification for this waveform generator. Also, 40dB correlates to 1% on the table.
Change in dB | Change in % | Change in dB | Change in % | Change in dB | Change in % |
10 | 31.6 | 30 | 3.16 | 50 | .316 |
11 | 28.7 | 31 | 2.87 | 51 | .287 |
12 | 25.1 | 32 | 2.51 | 52 | .251 |
13 | 22.4 | 33 | 2.24 | 53 | .224 |
14 | 20.0 | 34 | 2.00 | 54 | .200 |
15 | 17.8 | 35 | 1.78 | 55 | .178 |
16 | 15.9 | 36 | 1.59 | 56 | .159 |
17 | 14.1 | 37 | 1.41 | 57 | .141 |
18 | 12.6 | 38 | 1.26 | 58 | .126 |
19 | 11.2 | 39 | 1.12 | 59 | .112 |
20 | 10.0 | 40 | 1.00 | 60 | .100 |
21 | 8.90 | 41 | .890 | 61 | .890 |
22 | 7.94 | 42 | .794 | 62 | .794 |
23 | 7.08 | 43 | .708 | 63 | .708 |
24 | 6.31 | 44 | .631 | 64 | .631 |
25 | 5.62 | 45 | .562 | 65 | .562 |
26 | 5.01 | 46 | .501 | 66 | .501 |
27 | 4.47 | 47 | .447 | 67 | .447 |
28 | 3.98 | 48 | .398 | 68 | .398 |
29 | 3.55 | 49 | .355 | 69 | .355 |
Power Outage
What happens if I lose power to my computer, controller, and shaker amplifier?
The more recent versions of VibrationVIEW store data in a Temp folder even if “Save data to disk” is not selected on the Data tab in the test settings. The auto-saved Temp file is saved at the time interval set on the Data tab, even if the checkbox is not selected.
To retrieve the saved data, navigate to the Temp directory and select the last saved data file, which is named with a time stamp. The default is C:UsersusernameAppDataLocalTemp (How to show hidden files, folders, and drives in Windows 10/11).
Refer to the time history or print a report to determine how long the test ran. This information will give you a starting point to continue with the test. You may have to reset your amplifier prior to restarting the test.
What happens if I lose power to my shaker and controller but have UPS backup on my PC?
After the test stop code message “Lost Contact with IO box s/n” appears, you can resume the test as long as power is restored to the amplifier and controller. Otherwise, the data can be manually saved by selecting the Save Data button.
You can also retrieve the data by navigating to the Temp directory and selecting the last saved data file, which is named with a time stamp. The default is C:UsersusernameAppDataLocalTemp. (How to show hidden files, folders, and drives in Windows 10/11).
If you have data set to automatically save at the end of the test, then all information will be saved up to the time that a communication error occurs. You may have to reset your amplifier prior to restarting the test.
What happens if the accelerometer cable breaks while a test is running?
The controller will gently stop the test to prevent transients from passing through your shaker. A stop code with a message similar to “Max acceleration on Ch X” will appear.
Help & Support
How can I use Network Logging for technical support?
The Network Logging feature allows the Vibration Research technical support team to better diagnose communication issues you may have between your I/O unit and control PC.
To enable this feature (version 4.1.10 or later), select Configuration > Hardware. Select “Enable Network Logging (for technical support use).”
To send an information log to Vibration Research for assistance:
- Select Help > Help with current test.
- Fill in the questions and contact information.
- Select Request Help.
If you cannot connect the software to the I/O unit, navigate to the C:VibrationVIEW directory and email the file named “socket.log. C:Program FilesVibrationVIEWsocket.log.”
Training
Where do I register for user-training seminars?
See our User-Training Seminars page.
Our seminars are ideal for engineers, test technicians, application engineers, and others who seek to understand the basics of the Vibration Research software as well as the advanced applications and features. The presented topics cater to users of the VR8500, VR9500, and VR10500 vibration controllers and the ObserVR1000 dynamic signal analyzer.
Onsite training is also available. Call Vibration Research Corporation at 616.669.3028 or email vrsales@vibrationresearch.com for a quote.
When is the next free monthly webinar?
See our Free Monthly Webinars page.
Vibration Research is pleased to provide our customers with free webinars held each month. These courses are scheduled for 1 hour; all you need is a web connection and a phone.
You can also browse our Webinar archive.
I’m relatively new to the industry and would like to learn more. How do I get started?
Our goal is to make it as easy as possible for new users to get comfortable with our software, and we welcome feedback. There is a comprehensive Help file in the software that walks through the software features and provides tips for vibration testing and analysis. We also offer practice exercises, instructional videos, and a personalized learning dashboard that empower learners to study at their own pace.
Our library of resources includes:
- Vibration Research University
- Articles
- Quick Tip Videos
- Papers and Experiments
- And more