At the start of 2022, the Vibration Research team set off in nine small groups to test the ObserVR1000 dynamic signal analyzer in real-world applications. The goal was to understand our product better in an operational setting and note any potential improvements. The groups presented their findings to the rest of the VR team. This series relays pertinent (or simply fun) information we found.
How Data Collection Errors Impact Data and How to Deal with It
ObserVIEW Software: FDS, Waveform Editor, Multimedia Sync
Group 1 had big ideas for data collection, but plans kept falling through. Ultimately, they recorded a 30-minute helicopter ride.
However, in their haste to secure a project, there were several mistakes in preparation. Like all good scientific research, the group reported the issues and took notes for future test setups. The following are some of the lessons they learned.
Accelerometer Mounting Method
When recording data, it is important to consider the various methods of mounting the sensor(s). In a vibration test setup, stud mounting is preferred. However, this method is not usually feasible in a recording setting.
Instead, test engineers often opt for an adhesive such as glue or wax. Both options can obtain an excellent data response depending on the recording surface.
Group 1 mounted an accelerometer to the door of the helicopter with beeswax. Wax is a convenient adhesive and is generally applied in short-term situations. However, wax adhesives depend on temperature, surface material, and preparation.
In this instance, the beeswax did not hold, which lead to distortion in the recorded data. The data had artificial peaks and data were missing.
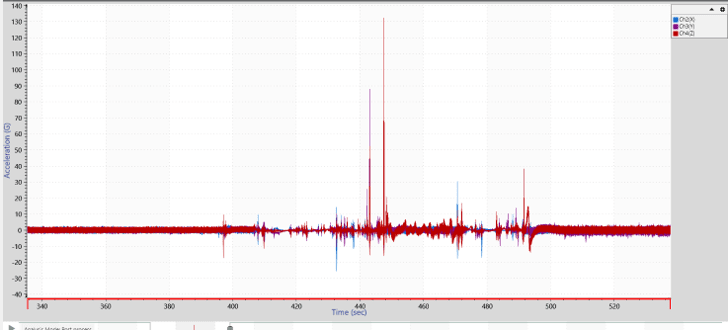
Data with artificial peaks between 440 and 460 seconds where the accelerometer detached.
Afterward, the group questioned if the peak errors affected the overall data. They took equivalent sections of unaffected and affected data and generated a fatigue damage spectrum (FDS) for both. The FDS generated from the data with the acceleration peaks displayed excessive damage.
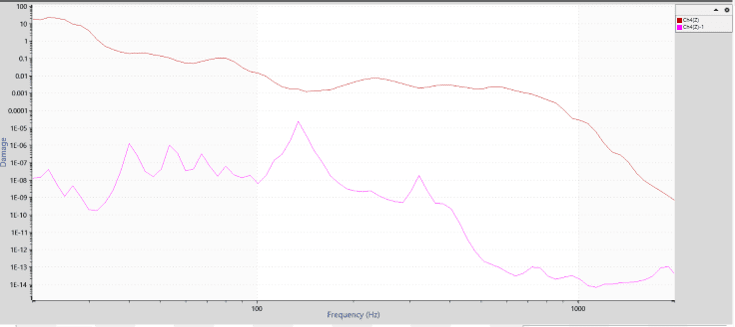
Excessive damage in the data.
Using the waveform editing tool in ObserVIEW, the team cut out the spikes to more closely reflect the operational environment.
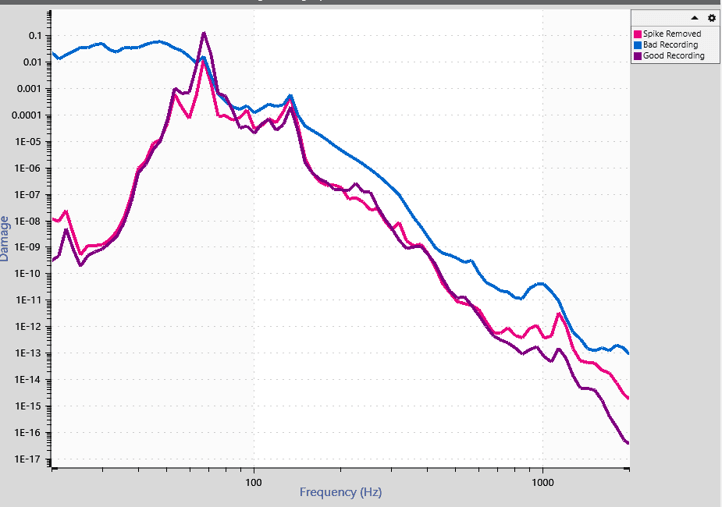
Data with the acceleration peaks removed.
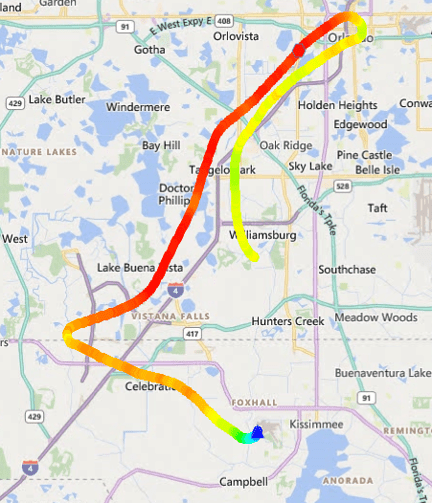
Satellite GPS data with a portion missing.
GPS Error
The GPS was not configured for a portion of the helicopter flight, so GPS data was missing. Luckily, the group was able to collect GPS data with the FlightAware flight tracking platform.
Sync GoPro and ObserVR1000
Group 1 also forgot to synchronize the GoPro and ObserVR1000, so there was an offset in the camera video and waveform data.
In the VR Mobile application, you can view the time settings on the I/O unit, any connected phone, tablet, or PC, and other recording devices such as a GPS. If the time is out of sync, press the Sync Time button to synchronize the I/O unit time to the correct time.
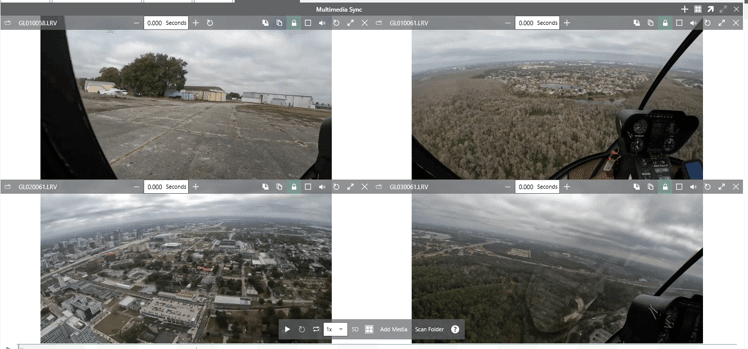
Thumbnails of the GoPro video from the flight.
Corrected Recordings
The group was able to address some of the recording errors in post-processing. The following is a comparison of the original data to the updates.
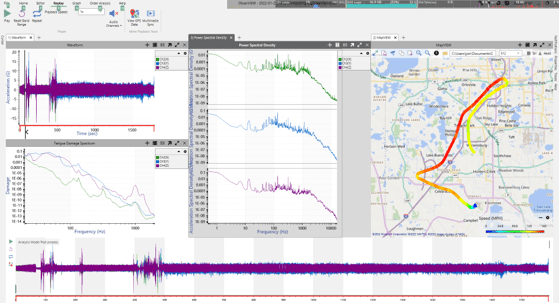
The original recording and supporting data with errors.
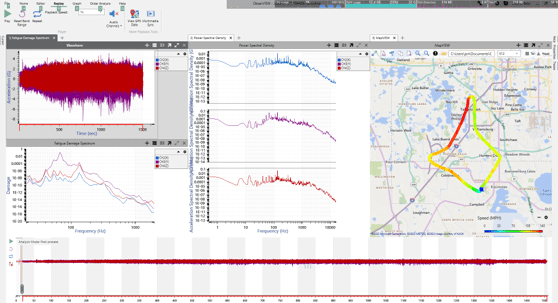
The updated recordings with edited waveforms and complete GPS data.
Featured Software
ObserVR1000 Recording Checklist
There are a few items to keep in mind when setting up the ObserVR1000 for recording. To make it easy, we’ve compiled a checklist to review before you begin.