Shock testing assesses a product’s ability to survive a transient event by running a sharp transfer of energy through a system. In physics, when a force acts upon an object and causes displacement, the object acquires mechanical energy. As such, some may use “mechanical shock testing” to describe this transfer of energy.
Unlike impact testing where the event is uncontrolled, a mechanical shock test defines the pulse’s shape, duration, and amplitude. Mechanical shock tests include pyrotechnic shock, drop shock, and free-fall shock. An example of a classical shock test definition is: “3 – 10mS, 20Gpk, half-sine pulses in all six orthogonal axes for a total of 18 shocks.”
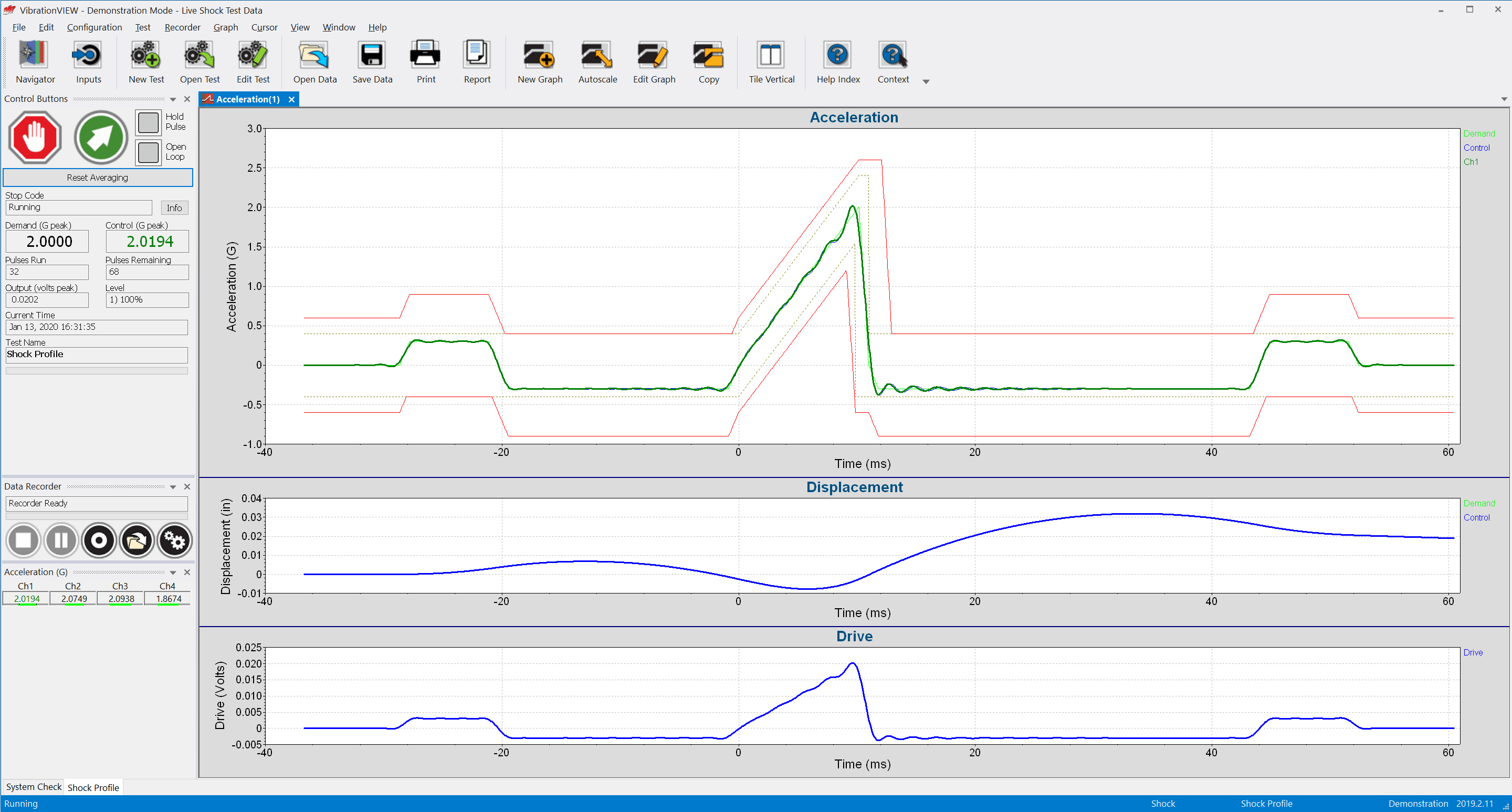
Example of a terminal peak shock pulse in the VibrationVIEW software.
What is the Difference between Vibration and Shock?
To understand mechanical shock testing, it is helpful to learn the difference between vibration and shock. At first, the two might seem interchangeable, as testing software is often packaged as “vibration and shock testing.” However, vibration and shock have several distinctions.
Vibration is a response to an excitation that oscillates about a reference position. It can be periodic, meaning continuous repetition, or random. When we record vibration, the output is a waveform over time. Then, the time waveform can be converted to the frequency domain to determine the source of unwanted vibration.
Shock is a sudden pulse exerted onto a system. The technician defines the shape of the pulse and its peak amplitude and duration. A shock test may run multiple pulses, but each is independent of the previous. While a vibration test identifies issues from consistent vibration, a shock test assesses a structure’s ability to withstand a short burst of energy.
Closed-loop Systems
Vibration testing runs on a closed-loop system. These systems include a vibration controller directed by a software platform to interact with a power amplifier, shaker, and one or more sensors.
The controller sends a signal to the power amplifier driving the shaker. It forms the drive signal by comparing the measured acceleration of the device under test (DUT) to the desired demand reference. This self-contained input/output forms a control “loop,” where the DUT’s response influences the drive signal.
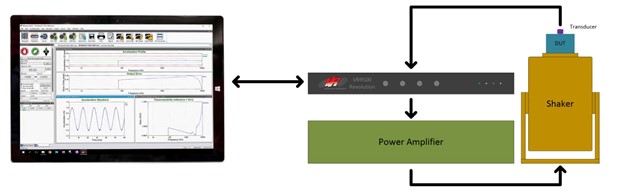
Diagram of a closed-loop system.
Mechanical Shock Machines
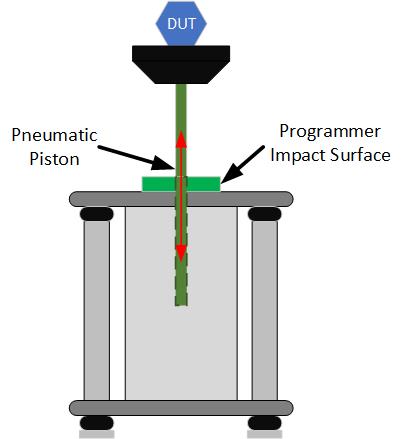
Diagram of a pneumatic shock machine.
Technicians can run shock tests without closed-loop control on mechanical shock machines. These machines excite a test table that the product is mounted to and include drop-shock machines, lightweight shock machines, medium-weight shock machines, and the Hopkinson bar. Technicians can change the test parameters by adjusting the speed of the machine’s movement or the effect of its movement on the product.
Shock Testing on Shakers
An electrodynamic or servo-hydraulic shaker can also generate many classical pulse shapes and can be a cost and time-efficient option for a routine test.
However, when a shock machine generates a classical shock pulse, some mechanical method stops the table. Vibration shakers do not have mechanical stops for this purpose. Additionally, shakers can generate only a fixed amount of velocity and displacement. To address this limitation, the shaker controller employs a process called compensation.
Learn more: Classical Shock Tests on Shakers
Complex Shock Testing
Mechanical shock tests generate a reliable and straightforward response for product evaluation and durability testing. However, a shock event may call for more complexity. Specialized software packages such as Shock Response Spectrum (SRS) are designed to re-create complex pulses.
Many synthetic pulses can represent a complex transient waveform with a frequency response comparable to the operational environment. It is also possible to replicate a signal from a recording and process it using an iterative shock control loop to generate and control the complex waveform.
Software for Mechanical Shock Testing
With Vibration Research’s Shock software, access standard classical shock pulses and vary pre/post-pulse compensation amplitude and shape. Alternatively, select the user-defined transient option to build a pulse from a recorded waveform. Advanced options include transient waveform control, SRS, and seismic testing.