The National Aeronautics and Space Administration (NASA) published NASA-STD-7001 to make uniform “the vibroacoustic verification process for spaceflight payload hardware.” The standard defines vibroacoustic activity as high-level acoustic noise from a flight that runs through the payload as acoustic excitation or random vibration. It applies to spaceflight payload hardware only, meaning an article carried by aircraft such as a satellite, spacecraft, or observatory.
NASA-STD-7001 is accessible to the public on the organization’s website. The most current version is 7001B, which superseded version A in 2017.
Flight Article Verification
Engineers perform several verification tests throughout the process of designing and manufacturing spacecraft. Verification determines if a test article can withstand the mission’s environmental conditions and identifies potential defects. NASA-STD-7001 provides test factors for “qualification, protoflight, and flight acceptance” verification methods.
- Qualification verifies the design of a flight article. It uses a stand-in item built like the flight article and exposes it to more severe conditions than the expected mission levels (with a margin to cover variations in build).
- Acceptance verifies the construction of a flight article. It tests the article in conditions similar to or slightly above the expected mission levels.
- Proto flight also verifies the construction of a flight article using qualification test levels and acceptance test durations.
An acceptance test requires a qualification test of the same design to establish a design margin. A proto flight test is selected when no qualification hardware is available, and it aims for little to no over-testing to avoid damage to the flight article.
The standard also includes parameters for workmanship tests, which verify the adequacy of a component’s workmanship before a flight.
Test Levels
Primarily, NASA-STD-7001 specifies acoustic and random vibration test levels in relation to the maximum expected flight level (MEFL). The test levels determine the severity of the test. The standard also includes test duration and control tolerances.
The following is a summary of the test requirements.
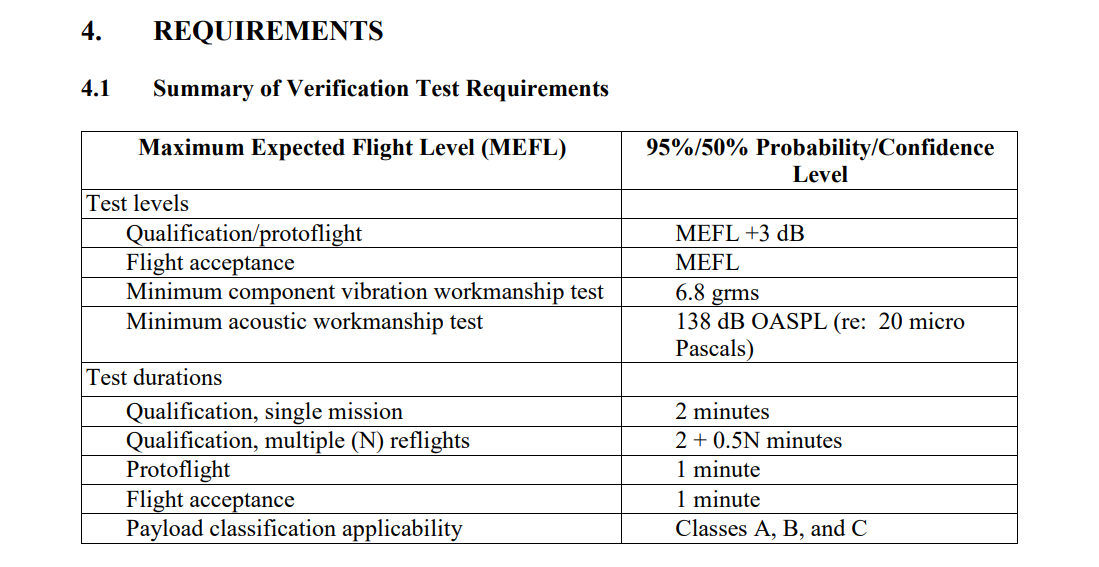
NASA Technical Standard: Payload Vibroacoustic Test Criteria, NASA-STD-7001B
Enveloping
NASA-STD-7001 requires that qualification, prototype, and acceptance tests “shall be conducted at levels that envelope the MEFL.”
The engineer derives the MEFL from measured data, either recorded or hypothetical. For greater control of random data, they derive an enveloped PSD to smooth out the peaks. The maximum envelope uses the maximum value at each frequency rather than average acceleration. Then, they increase the levels to the 95% probability/50% confidence and add the tolerances provided by the standard.
Tolerances
Test control tolerances help maintain proper levels. If a control channel exceeds its limit, the vibration controller adjusts the drive until the input returns to appropriate levels. NASA-STD-7001 provides the following tolerances for vibroacoustic testing.
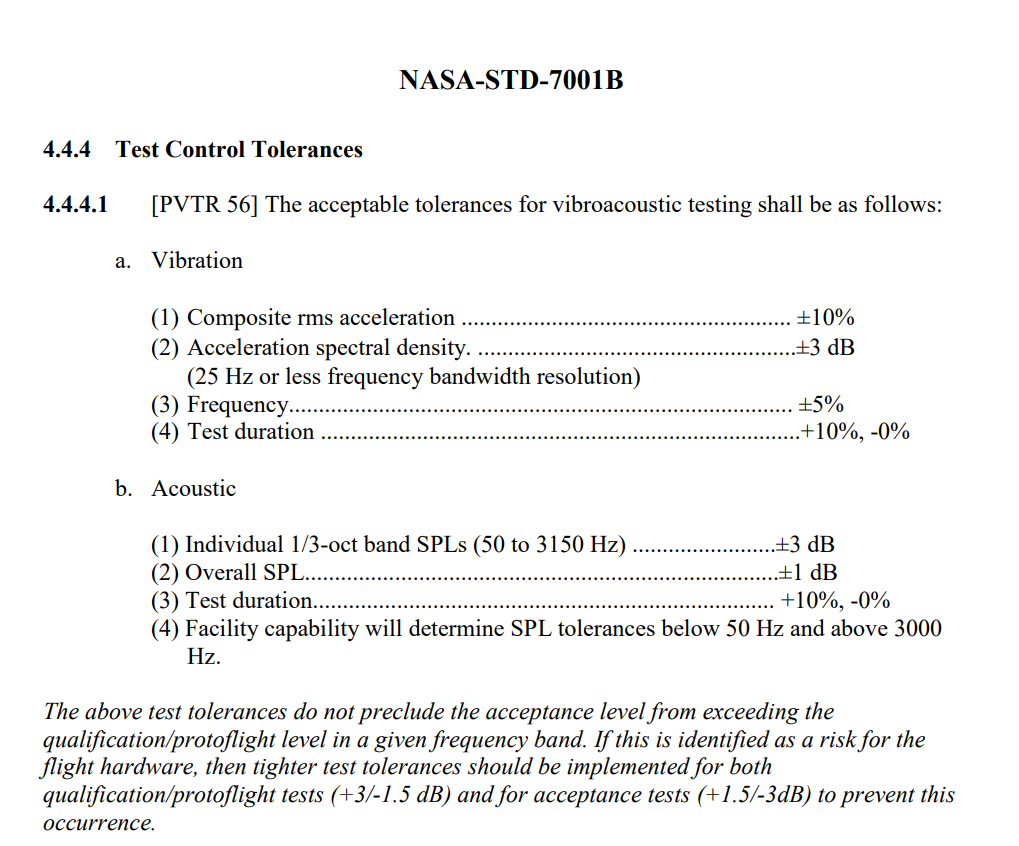
NASA Technical Standard: Payload Vibroacoustic Test Criteria, NASA-STD-7001B
Notching and force limiting are more specialized limiting functions, and the standard also provides guidance on them.
Acoustic Tests
Acoustic tests are typically performed in a test chamber, where controlled sound waves strike the test article at frequencies above 100Hz. The acoustic response is measured in sound pressure levels (SPL), which indicate alterations in the pressure of the sound waves. It is a ratio of the sound pressure to a reference sound level (the most common reference is 20 μPa.)
NASA-STD-7001 requires an acoustic test at the payload level of assembly and for all hardware susceptible to an acoustic environment. The preferred test setup includes a reverberant chamber, but a direct field acoustic test (DFAT) is an acceptable alternative.
The standard calls for control of SPL (dB re 20µPa) in 1/3 octave bands over the specified frequency range. When an acoustic signal’s frequency range is fractioned into eight bins, engineers refer to the sections as octave bands. One-third octave bands are an arrangement of twenty-four frequency bins. The standard allows for control of higher octave bands that meet or exceed the requirement.
The number of microphones and their placement should depend on the test article’s size, configuration, and surface space. However, a minimum of 4 microphones is recommended for reverberant acoustic testing.
Please see section 4.2.1 for all details.
Random Tests
Random vibration tests are performed on a closed-loop system. The test item is mounted to a shaker, and a vibration controller outputs a drive signal to the shaker. The random test profile determines the drive signal, and the hardware controls the signal based on the shaker table/test item’s response.
The random test profile is arranged in a breakpoint table, which includes frequency (Hz) and amplitude (G^2/Hz) values and the crossover slope (dB). The power spectral density (PSD) plot displays the values; a change in PSD levels is measured in dB.
NASA-STD-7001 requires a random vibration test for all hardware susceptible to mechanically transmitted random vibration. The test should be run in the three orthogonal axes: x, y, and z. It calls for control of the PSD in frequency bandwidths of 25Hz or less over a frequency range of 20 to 2,000Hz.
Please see section 4.2.2 for all details.
Additional Details
The standard also includes details on how to configure the test item for testing and options for test tailoring. Furthermore, it provides information on recording and analyzing the test data. Data analysis separates data for further evaluation. Engineers can use it for resampling and filtering waveforms, identifying level changes and resonances, determining the cause of test item fatigue or failure, and more.
Spectrometer Vibration Test
Commercially available technology such as the tested spectrometer is effective for staying within budget constraints. Space-qualified spectrometers are on the order of $100K each while off-the-shelf spectrometers cost significantly less.
However, maintaining a budget is meaningless without confidence that the off-the-shelf technology will survive a launch. For a spectrometer vibration test, engineers can implement NASA-STD-7001B.
For more information on small satellite vibration testing applications, please visit the software page.