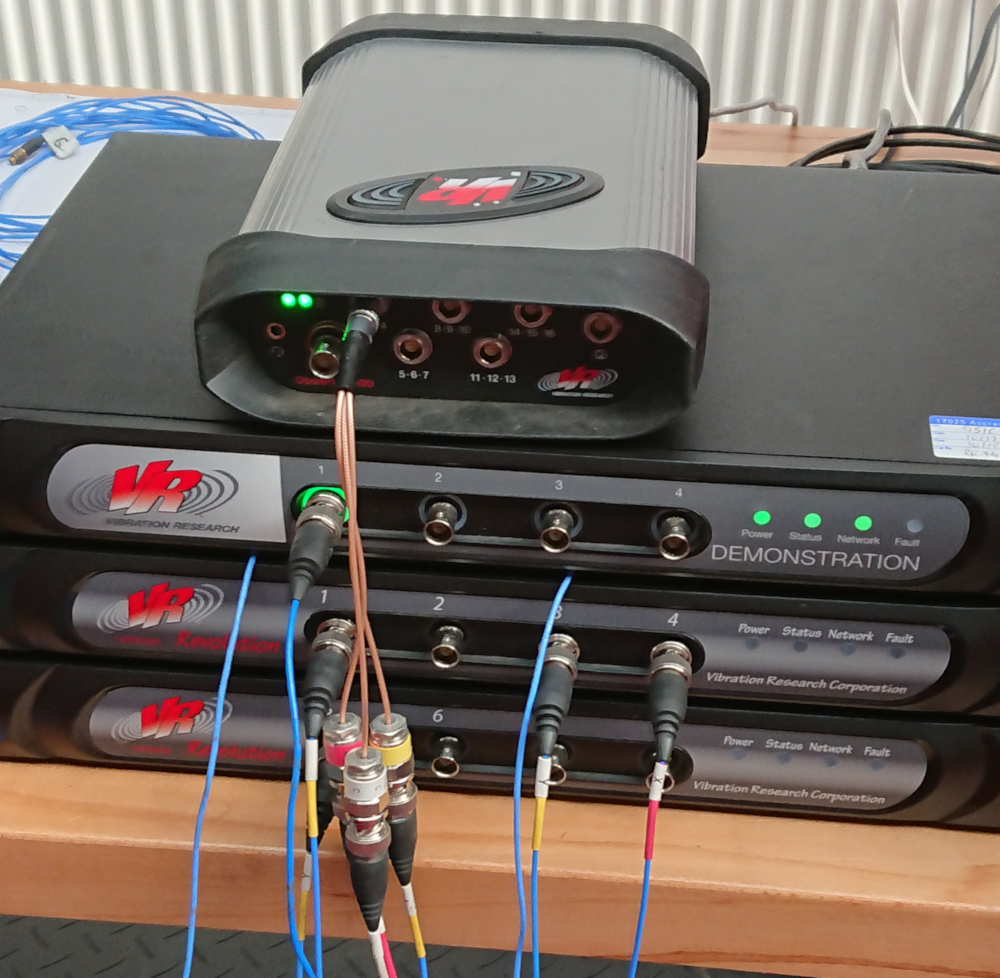
An ObserVR1000 setup for independent measurement.
Engineers may add a device to their vibration control setup to perform an independent measurement. Typically, industries like aerospace employ this option when the device under test (DUT) is expensive, sensitive, or volatile. Independent measurement helps engineers validate assumptions, ensure accuracy, and verify the success of their vibration control.
Verification of Control
For closed-loop vibration control, the controller sends a signal to the shaker, and the sensor(s) sends the control response back to the controller. The controller adjusts its output based on the response to maintain a pre-defined vibration level.
Engineers can compare control and independent data to verify whether the implemented measures effectively control vibration on the shaker table.
If there are no deviations, cross-checking the measurements validates the test data. Many industries require vibration tests to adhere to specific standards or regulations, and independent measurements provide objective data for compliance assessment and reporting.
Otherwise, independent data can help the engineer investigate the control error. For critical testing, engineers can monitor the data as the test is running and stop the test if there is a measurement discrepancy.
Calibration and Sensor Performance
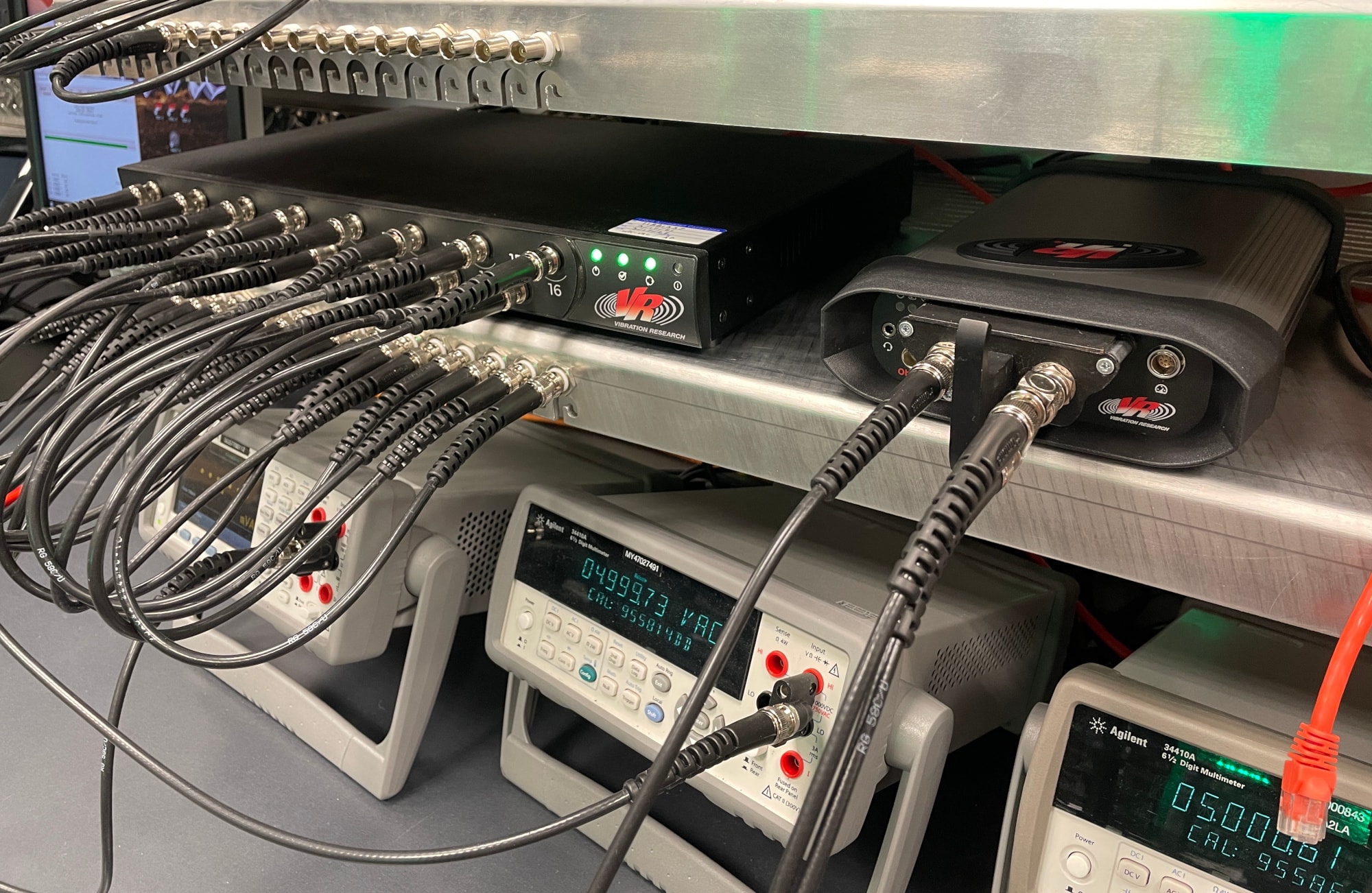
VR recommends an annual calibration for sensors and controllers.
Equipment performance is one potential source of control error. Independent data can confirm the accuracy and reliability of a measurement instrument, such as a sensor or controller. Comparing measurements to an independent source can help identify potential calibration issues or sensor drift.
Calibration ensures that equipment measurements are accurate within the specification limits. Over time, measurement readings will drift. Calibration will either confirm that the equipment’s readings are in-tolerance or adjust the equipment if out of tolerance.
Engineers can use an independent measurement as a part of a preventative maintenance plan or as a method for determining a calibration schedule for a controller. Vibration Research recommends an annual calibration for sensors and vibration controllers, although a laboratory may do so more frequently depending on its needs.
Validation of Models and Simulations
Engineers often use models to simulate vibration control, which independent measurements can validate. If the data match the predicted outcomes, it instills confidence in the accuracy of the simulations.
Additionally, mechanical systems can exhibit complex dynamic behavior that simulations do not capture. Engineers can use independent measurement to record the DUT’s interactions, non-linearities, and time-varying characteristics to improve models.
Independent Measurement for Vibration Control
With the ObserVR1000
The ObserVR1000 is a portable, lightweight data acquisition device: ideal for taking independent measurements. With up to 128 channels and a 128kHz simultaneous sample rate, it can easily process large data samples.
The ObserVR1000 can also connect to Live Analyzer in the ObserVIEW software for live streaming. Engineers can view data in real time and pause the live stream to select, analyze, and export a section of the time waveform. They can also monitor fatigue damage live with the Fatigue Damage Spectrum option.
Example Setup with the ObserVR1000
The following is an example setup for running vibration control while performing independent measurement with an ObserVR1000.
The setup included:
- VR9500 vibration controller
- 4-channel ObserVR1000
- Single-axis accelerometer (100mV/g) connected to the Ch1 BNC input
- Triaxial accelerometer (10mV/g) connected to the Ch2, 3, 4 LEMO input using a LEMO to BNC conversion cable
The single-axis accelerometer was mounted at the center for armature control. The triaxial accelerometer functioned as a DAQ-independent measurement. The DAQ device charged from the power mains.
Technical note: The accelerometer’s size and weight must factor in the properties of the measured structure. The accelerometer should weigh 10x less than the structure to reduce the influence of its weight on the structure’s dynamic properties.
Two IEC 61300-2-1 tests were performed on a shaker armature in the vertical direction since the slip table did not affect the data. In some cases, the slip table can influence measured and replicated signals.
Are you interested in what an independent measurement setup might look like for your laboratory? Contact us!