The shock response spectrum (SRS) is a valuable test tool for products/structures that experience complex transient shocks. However, as the SRS is a theoretical model and a pass/fail test, engineers often encounter several of the same problems during testing. Below, we discuss three common control errors and their solutions in the VibrationVIEW software.
For more information about the SRS, watch the Fundamentals of Shock Response Spectra (SRS) tech talk.
Pulse/Test Never Reaches Full Level
The SRS is typically a pass/fail test, meaning all waveform points must be at or above the demand. When the test requires that the tolerance “shall meet or exceed the demand,” the minus tolerance must be equal to the demand. If an underlying wavelet is below it, the test will not count the pulse as valid or enter Run mode at all.
Solution
In VibrationVIEW, the user can review each underlying wavelet to determine which is below the demand and adjust it manually. However, there is a quicker solution.
On the SRS tab, the user can synthesize an SRS pulse to meet or exceed the demand line. To exceed the demand by a set percentage, navigate to the SRS Synthesis section and adjust the “Exceed SRS demand by” field. This option adds an excess margin above the defined breakpoint table (required response spectrum) when generating a control pulse (test response spectrum). The exceed demand is a synthesis parameter, so the user must select Synthesize or Iterate More after adjustment.

The “Exceed SRS demand by” field on the SRS tab.
Minus Tolerance
Some SRS test specifications allow for a “minus tolerance.” This means some percentage of the control can be a certain level below demand. For example, it is usual to see a specification that requires 90% of the lines to meet or exceed the demand, meaning 10% of the points can be less.
Further, some specifications allow lines that are lower than the product’s first resonance to be out of tolerance. For example, a specification could have a demand from 5Hz to 2kHz, and the primary resonance of the device under test is 100Hz. Others may allow lines below 50% of the primary resonance to be out of tolerance. The user should synthesize waveforms that are deliberately below the tolerances at low frequencies to minimize the displacement of the test.
Initial Pulse Overshoots
A test’s drive limits determine the drive voltage output at different stages. The starting drive limits apply while the controller is equalizing the pulse. The test will abort if the maximum voltage is exceeded in the positive or negative direction.
During a low-level SRS test, the initial pulse can overshoot the SRS limit. This problem stems from the test profile or the amplifier’s gain settings. If the amplifier or output threshold voltage is too high, the initial pulses can overshoot the demand.
Solution
Decreasing the maximum starting output will limit the voltage of the startup pulse, ensuring that the first pulse is not too high. To do so in VibrationVIEW, navigate to the Limits tab in the Test Settings dialog box and adjust the Max Output field under “Starting drive limits.”
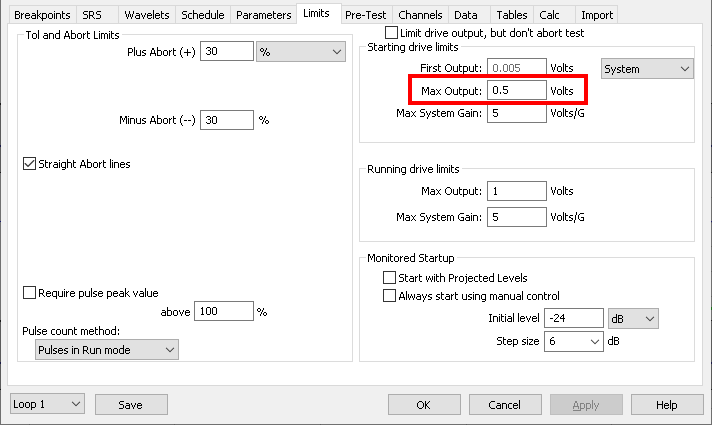
The Max Output field on the Limits tab.
Resonance Causes SRS to Exceed Tolerance
Resonance in SRS testing occurs when the vibration of one of the pulse’s underlying wavelets matches the natural vibration of an SRS substructure, amplifying its response.
Solution
The VibrationVIEW software automatically adjusts the wavelets’ amplitude values to achieve the desired SRS profile. This action includes pulling down wavelets that exceed demand due to test resonance. In other software packages, the user must manually adjust the wavelets.
Contact Support
Are you still experiencing a problem with an SRS test? Our support team is ready to help.