VibrationVIEW Software Package
Sine
Random
Fatigue Damage Spectrum
Test Acceleration
Mixed Mode
Sine Resonance Track & Dwell (SRTD)
Kurtosion
3-axis Control
Four-post Control
Customized Vehicle Test Profiles
Generate test profiles or enter specifications with ease. The VibrationVIEW interface is intuitive and user-friendly, and the software is industry-leading. Access standard vibration testing modes built for ease of use and advanced features you won’t find anywhere else.
Autonomous Data Acquisition
OBSERVR1000 & VR MOBILE
The ObserVR1000 hardware can be controlled remotely with the VR Mobile application, which runs on a smartphone or tablet using a WiFi connection. Set up, monitor, and modify field data recording without a wired configuration.
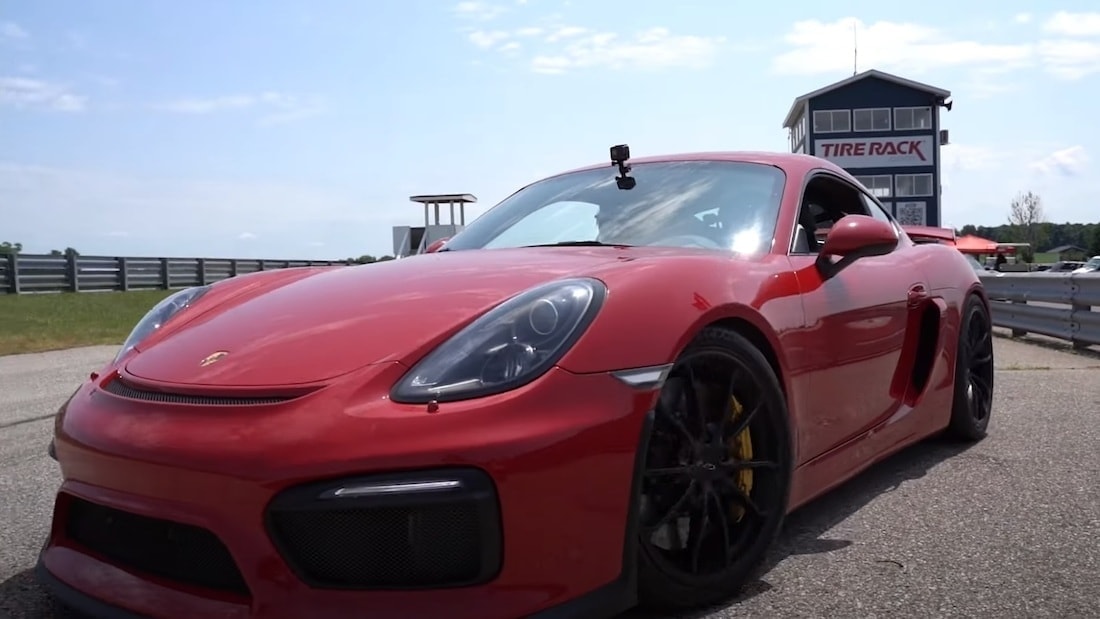
MONITOR TESTS REMOTELY: Observe live data recording from any mobile device. Select, start, and stop the test; analyze issues with a live FFT display.
SET UP AUTONOMOUS ACQUISITION: Define any number of triggering events to record data without interference. Save processing time, capture transient events, drive external equipment, and more.
CONNECT A TACHOMETER: Configure a dual or quadrature tachometer to measure rotation. Encoder types include wheel, rotational, or scalar.
DISPLAY GPS DATA: View position updates at about 1Hz along with GPS timebase synchronization. Then, play the GPS media files in sync with a waveform recording.
Multi-axis Control
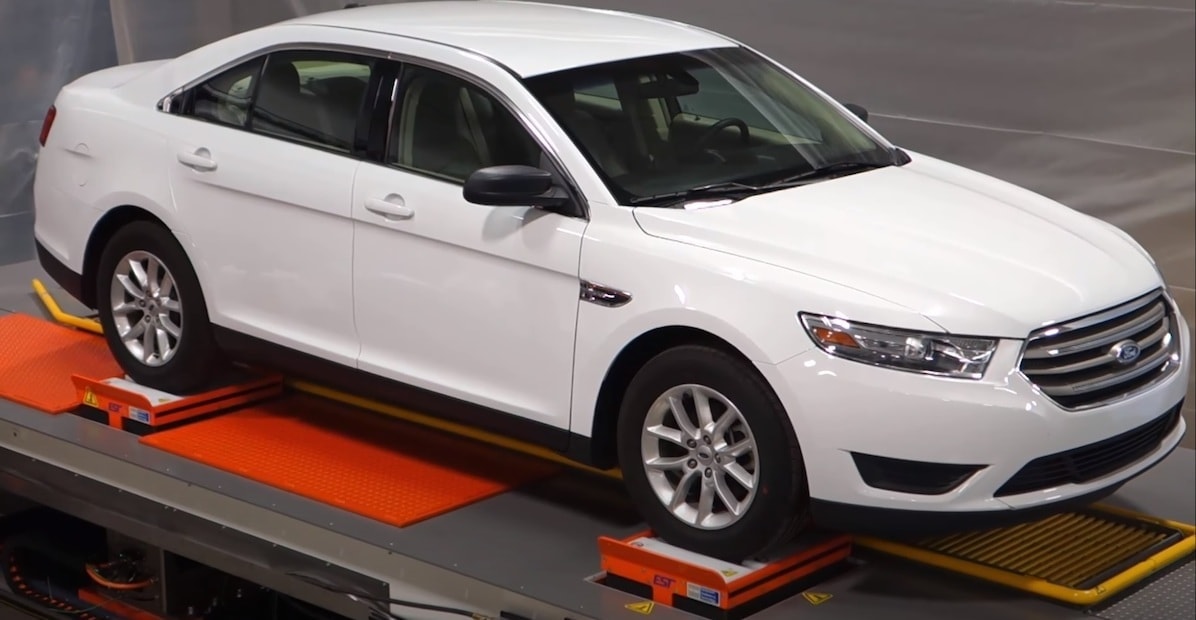
Replicate Field Data
VibrationVIEW offers several test development methods to replicate the original environment of a product using recorded data. The result is a test profile that closely reflects—or is equivalent to—the field environment.
NVH Testing
NOISE, VIBRATION, AND HARSHNESS
Automotive manufacturers depend on noise, vibration, and harshness (NVH) testing to optimize vehicle performance and maintain a standard of comfort across their vehicle catalog.
Vibration Control
Mix & Match Controllers with Shakers
Control modules can be used independently on separate shakers or linked into a single stack for jobs requiring a higher channel count (up to 512 channels total).
This cost-effective solution creates substantial savings for our customers.
Copy > Paste in Excel & Word
Copy and paste vibration test profiles and graphs between VibrationVIEW and Microsoft Word/Excel. This feature is especially useful when sharing profiles with colleagues, entering data from a customer, or entering lengthy or complicated test profiles.
Electric Vehicle Testing
The automotive industry has made many advancements in this growing sector, particularly in battery electric vehicle (BEV) development.
EV vs. ICE
The team at VR recorded data from an electric and internal combustion vehicle to better understand the differences in their noise, vibration, and harshness.
EV Battery Standards
Several organizations have developed EV battery testing standards, including the International Electrotechnical Commission (IEC), the International Society of Automotive Engineers (SAE), and the United Nations (UN). Learn more about these standards.
EV Battery Drop Shock Test
Drop shock testing is standard in the packaging industry but is applicable to many. Electric vehicle batteries (and other lithium-ion batteries) must meet international standards before shipment.
Industry Standards
ASTM Series | ISTA Series | ISO 10326-1 |
ISO 16750-1 | SAE J1211 | GMW3172 |
JIS D 1601 | MIL-STD-810 |
GMW Mirror Evaluation
GMW14201 is a rotational vibration measurement test for inside and outside automotive rearview mirrors and measures the mirror’s rotational response when subjected to vertical input vibration.
Buzz, Squeak, Rattle Testing
Vibration Research offers control hardware and shakers customized for low-noise operation used in BSR testing, sound limit testing, sound recordings, and anechoic chambers. The VR9500 and VR10500 controllers have a low noise floor (<70nV/√Hz) with a 130dB dynamic range. The controllers are compatible with all shakers and do not require a special board in the controlling PC.
Additional Features
- Control sine, random, or shock vibration to 50,000Hz
- 104,000 lines of resolution (26,000 with the VR9500)
- 24-bit analog inputs
Ford Motor Case Study
Lab technicians at a Ford Motor Company testing facility faced a puzzling and potentially dangerous dilemma. Were the company’s laboratory tests simply over-testing or were they accurately predicting a real and potentially dangerous situation? The facility used Vibration Research’s Fatigue Damage Spectrum software to solve its product challenge.
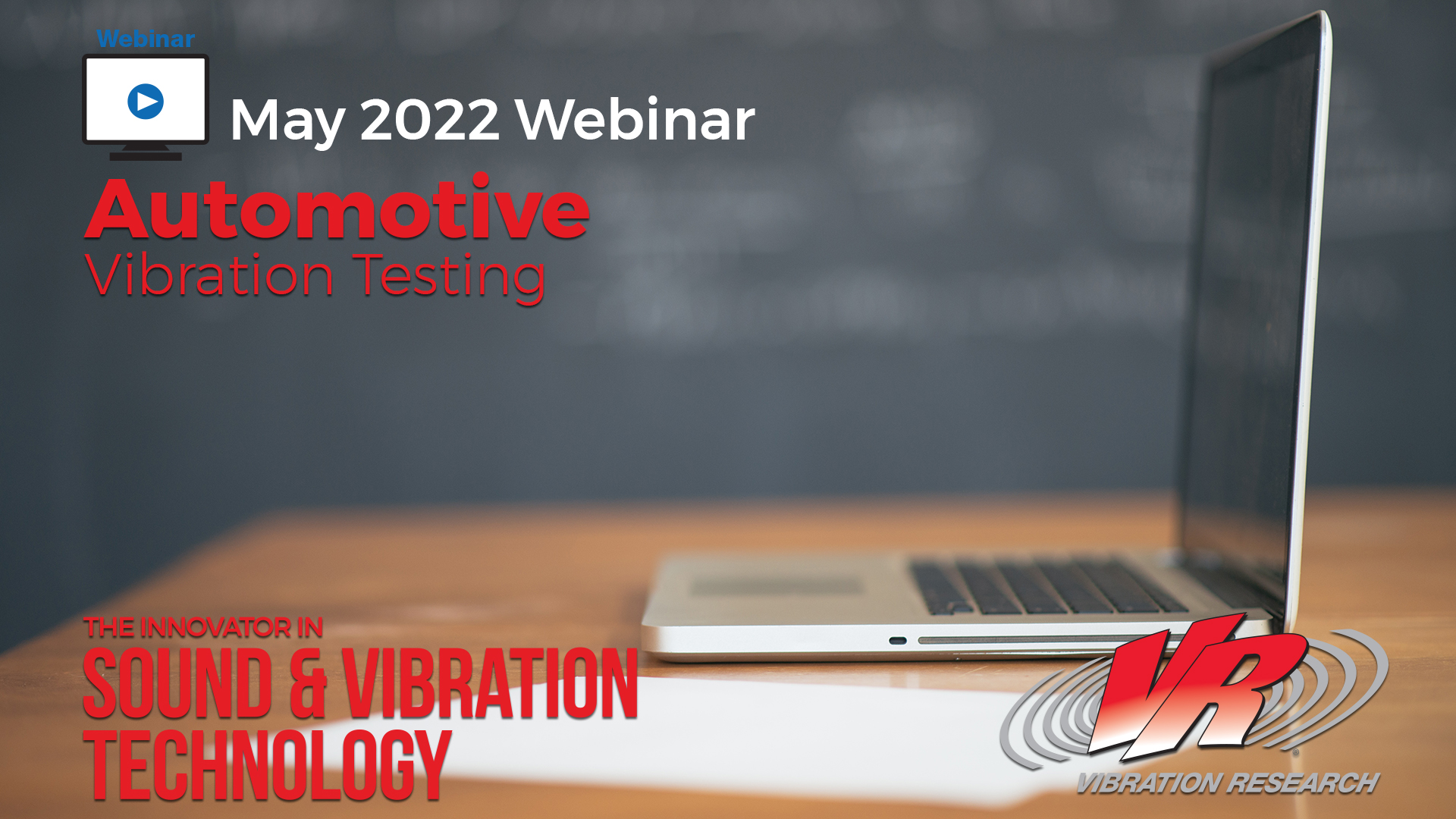
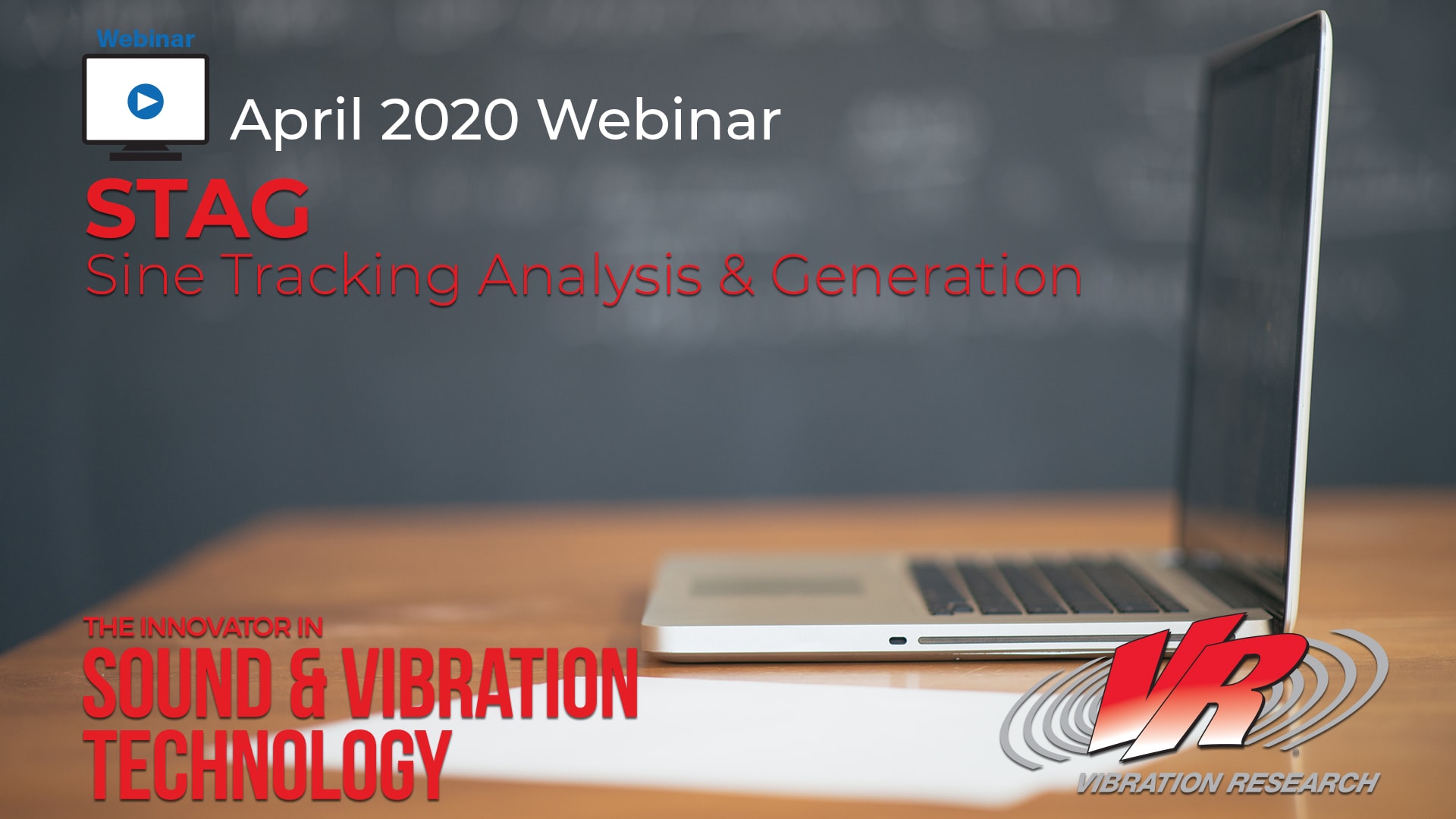
Data Recording & Analysis Applications
- Event Triggering
- Transient Capture
- Mobile Interface
- NVH and Whole Body Vibration
- GPS
- In-Vehicle Data Acquisition
- Video/Data Synchronization
- Order Tracking and Analysis
- PSD Analysis
- FFT Analysis
- Cross Spectral Density
- And more!
Vibration Control Applications
- Electrical and Electronic Components
- EV Battery
- Powertrain
- Interior Components
- Crankshaft SRTD
- Buzz, Squeak, and Rattle
- Random Acceleration
- Component Durability & Fatigue
- Transport Simulation
- Dual Axis with Phase Control
- Four Post Control
- And more!