VibrationVIEW Control
Set up and safely control vibration shaker tests using any VR hardware unit and generate custom reports. VR hardware works with any electrodynamic, servo-hydraulic, or servo-electric shaker and includes single-axis, dual-axis, dual-phase, rotational, three-axis, four-post, and seismic control options.
Record Field Data
Standard data and test specifications for battery vibration testing do not wholly represent the operational environment of automobiles. Developing a test with recorded data is the best way to produce a test profile that reflects the product’s intended use. Standards like SAE J2380 recommend using recorded data for test development when possible.
Autonomous Data Recording
Collect data with the press of a button using the battery-powered ObserVR1000 data recording hardware and the VR Mobile interface. Engineers can set up, monitor, and modify field data recording without a wired configuration.
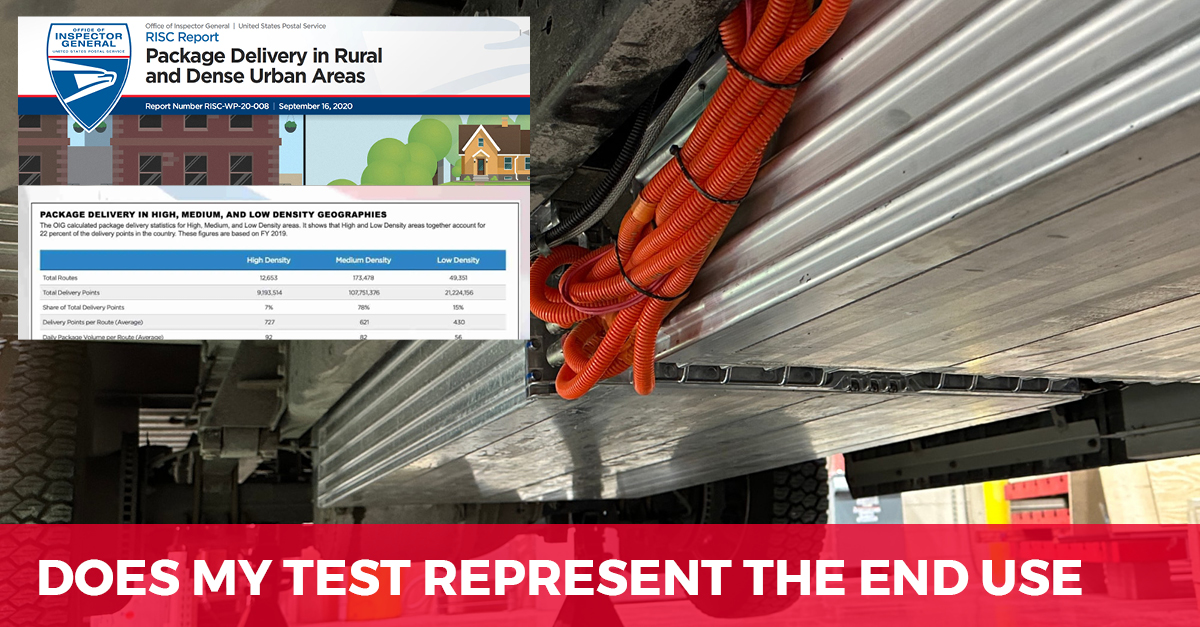
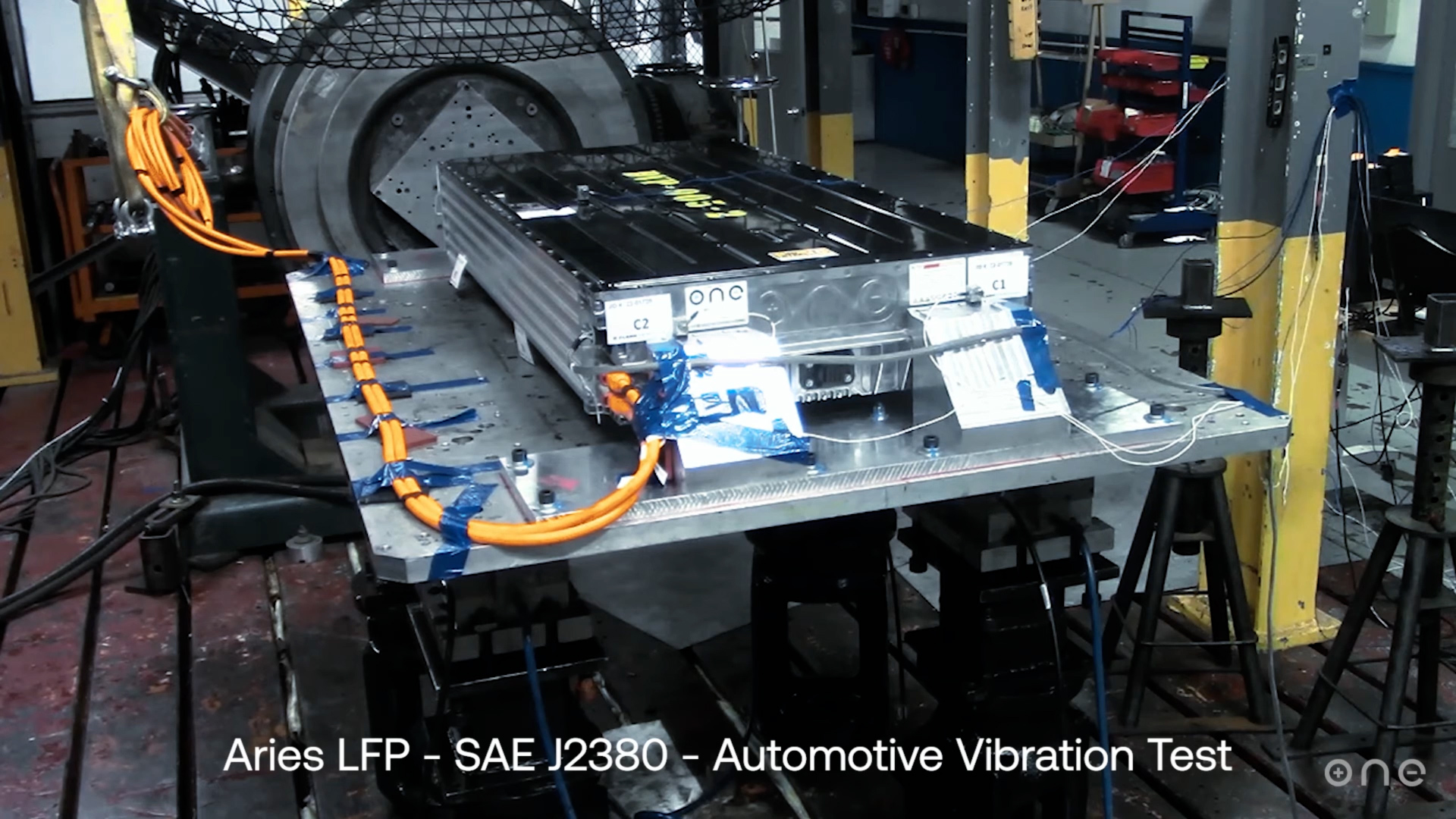
Photo courtesy of Our Next Energy
Test Development Tools
VR offers several test development methods to replicate a product’s operational environment using recorded data. The result is a test profile that closely reflects—or is equivalent to—the field.
Testing Standards
Several organizations have developed battery vibration testing standards for EVs, including the International Electrotechnical Commission (IEC), the International Society of Automotive Engineers (SAE), and the United Nations (UN). Learn more about these standards.
EV BATTERY DROP SHOCK TEST
Drop shock testing is standard in the packaging industry but is applicable to many. Mechanical abuse test programs for EV batteries often involve shock testing, including international standards for transportation.
High Channel Count Systems
VR10500 Vibration Controller
The VR10500 is a high-powered option for advanced vibration testing. VR engineered the VR10500 to coordinate with high-channel-count and multi-shaker systems.
- 16 channel count system (8 channel min.)
Up to 512 input channels
- Multiple shaker systems
- Controller and analyzer combination
- Advanced controller configurations
- Up to 6 outputs (4 analog/2 digital)
Control Averaging
VibrationVIEW can combine multiple control channels using the average of the selected channels. It does not limit the number of control channels for averaging, which is particularly beneficial when running a high-channel-count test on a large shaker.
Control Software Innovations
Instant Degrees of Freedom (iDOF)
Instant Degrees of Freedom (iDOF) employs an advanced algorithm to deliver accurate and low-variance PSD estimates that are calculated quicker than traditional averaging.
With iDOF, you can verify that the control PSD is within tolerance, determine how the test affects the DUT, and stop the test before the energy from a vibration resonance inflicts damage.
TruClip™
TruClip predicts the drive signal and removes peaks that would exceed the acceleration, velocity, or displacement limitations of the shaker.
TruClip helps engineers protect their device under test and shaker system, which is necessary for volatile or sensitive products such as batteries. For test profiles for large batteries, the engineer can avoid tripping the limits while running a random vibration test.
Monitor Test Status
With the Web Server and Email Notifications features, engineers can monitor a system’s status anywhere in the building or in the world with a mobile device. Send a notification to your email/cell phone at the end of a test or view the test live with the Remote Interface option.
Additional Safety Features
- Emergency stop: quickly stop a test without putting a transient shock into the test item
- Set tolerance and abort limits to detect inconsistent measurements
- Convert a thermocouple signal with an external conditioner for processing
- Monitor multiple tests simultaneously with the DashboardVIEW application
EV/Hybrid Powertrain Test Systems
The electric battery makes up a large part of an EV powertrain testing plan, but components work in tandem. Vibration Research offers many options for component and full-scale vibration testing, addressing challenges like real-world simulation, long test times, accurate measurements, and complex test configurations.
EV/Hybrid Powertrain Components
- Inverters
- Semiconductors
- Battery and battery charger
- Converters
- Power steering
- Transmission
- Motor and motor driver
- Combustion engine (hybrid)