The heater goes out. The lawnmower will not start. The propeller stops spinning. The vehicle’s engine fails.
All objects experience fatigue when repeatedly exposed to significant levels of stress. According to Miner’s rule of damage, fatigue accumulates over time. Fatigue damage is the result of multiple repetitions of low-level stress applied to an object. Generally, it occurs in three stages:
- Crack initiation
- Crack propagation
- Final fracture, otherwise known as the breaking point
This phenomenon differs from damaging events that exceed instantaneous stress limits, such as a glass vase shattering on the floor.
Fatigue Damage Analogies
River Analogy
As river water flows, it slowly erodes the riverbanks. The water might knock particles loose or carry other material, such as tree branches or sediment, that causes the erosion.
River water flowing at a higher velocity has more energy to dislodge rocks and pebbles from the riverbank soil. Consequently, a faster-flowing river will erode the riverbanks more quickly. If we know the rate at which the soil erodes under normal river flow, we can calculate the rate at which it will erode under the conditions of a faster-flowing river.
Paperclip Analogy
Suppose we want to break a paperclip by bending it back and forth multiple times. The paperclip has numerous bending modes; we can bend it back and forth with a maximum angle of 10°, 20°, 30°, and so on. One hundred bends at 10° plus 25 at 30° may cause the paperclip to break, meaning it has accumulated its life dose of fatigue. Thirty bends at 20° plus 40 at 40° might also accomplish the same outcome. Either way, according to Miner’s rule of damage, the paperclip has accumulated its life dose of fatigue. This occurrence is analogous to river water flowing at a constant rate with some combination of the water and sediments causing erosion.
These related analogies (river and paperclip) prompt several questions:
- How can we break the paperclip more quickly?
- How can we relate the bending paperclip to the increased flow of river water?
To answer these questions, we must change our analogy from bending the paperclip at various angles to vibrating the paperclip at various frequencies.
Suppose we find the main resonant frequency of the paperclip. If we vibrate it at the resonant frequency, we will reach the life dose of fatigue for the paperclip after a specific number of vibration cycles. To bring the paperclip to its life dose of fatigue more quickly, we must vibrate it at its resonant frequency with higher level accelerations (akin to water flowing with more speed or energy).
Ultimately, the paperclip will break when it experiences its life dose of fatigue, regardless of how it arrived there. It can accumulate gradually (low-level accelerations at the resonant frequency) or rapidly (high-level accelerations at the resonant frequency).
Fatigue Damage and FDS
Engineers can calculate the total fatigue damage an object experiences within a particular timeframe from the power spectral density (PSD), which represents the energy of a random vibration signal. Plotting this fatigue damage versus frequency produces a fatigue damage spectrum (FDS), a means by which to quantify the stress-strain loads put onto a product.
Water Bucket Analogy
The FDS indicates the amount of fatigue at each frequency in the spectrum that will bring an object to failure (Figure 2). Its total life dose of fatigue is the area under the FDS curve.
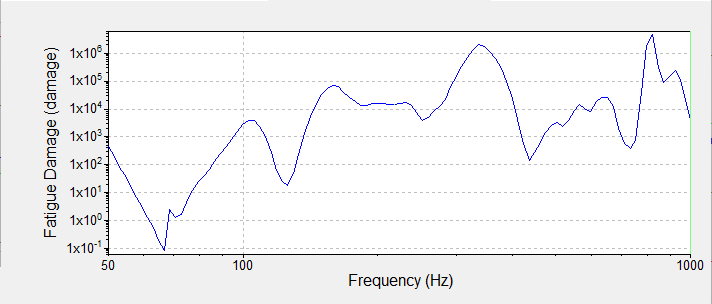
Figure 2. A typical FDS plot.
Let’s flip the plot upside-down to help visualize this idea from a different perspective (Figure 3).
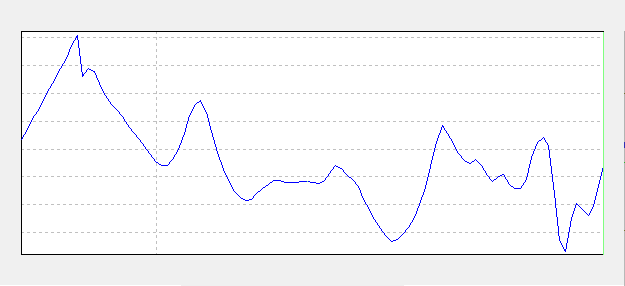
Figure 3. The inverted FDS in Figure 2.
The inverted FDS plot is like a bucket. If we fill the bucket with water (fatigue), then the object will be brought to failure when the bucket is full (life dose of fatigue). The amount of water necessary to fill the bucket represents the total life dose of fatigue (Figure 4).
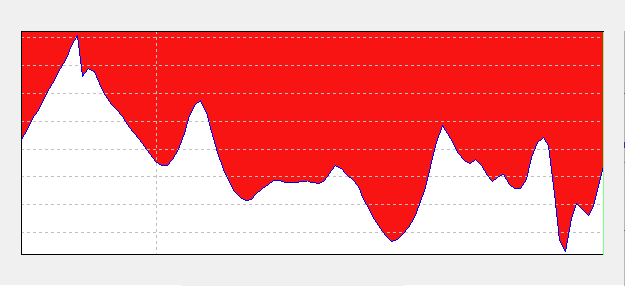
Figure 4. The inverted FDS in Figure 2. The red section indicates the total life dose of fatigue.
To accelerate the test (i.e., to bring the object to failure more quickly), we need to fill the bucket with water more quickly. The FDS test accomplishes this by applying higher energy levels (RMS) to the test. The goal is not to add more water to the bucket (increasing the amount of total fatigue) but to change the rate at which the water is added to the bucket (increasing the rate at which fatigue accumulates).
Putting a Product to the Test
Vibration-induced stress accumulates material fatigue, which is a leading cause of product failure. Vibration test engineers run products to their breaking point to determine how long they can withstand the end-use environment and to make design improvements. Engineers do not want to spend any more time than is necessary to reach these goals.
Engineers can use the FDS to statistically simulate a DUT’s end-use environment. FDS software can accelerate an FDS-generated random PSD test profile to a desired test duration by increasing system energy. It can also combine different vibration environments and weigh them based on their contribution to the life of the product in a standard environment.
FDS Software
Importing and Accelerating Tests
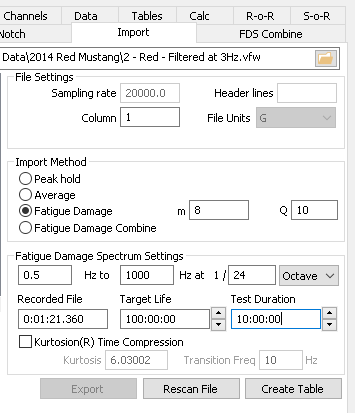
Figure 5. The Random Import tab in VibrationVIEW.
In the VibrationVIEW software, engineers can use the Random Import option to import recorded data. After they set the fatigue parameters (m and Q values) and enter the target life and desired test duration, the software can compute an FDS for the recorded file and its target life (Figure 5).
To accelerate the test, the engineer must select a shorter test duration. To bring the product to failure for this new test duration, the software must increase the root-mean-square (RMS) value, resulting in an increased PSD.
The FDS spectrum does not change with the new test duration. The total fatigue damage will be the same so long as the target life value does not change. Decreasing the test duration, however, will accumulate the total fatigue damage more quickly, which is accomplished by an increased RMS value.
Combining Different Environments
A simple vibration profile does not represent the real world, and products typically experience a range of environments. With Random Import, engineers can combine various vibration environments to simulate a product’s end-use environment more accurately.
To create a profile that combines all environments, engineers must adjust the target life to represent the relative amount of time the product spends under various conditions.
Engineers should enter a reasonable test duration when accelerating an FDS-generated PSD test profile. This new test duration value will increase the PSD and the RMS. The test must necessarily run at a higher RMS value to accumulate the life dose of fatigue faster.
Kurtosis Control
Engineers can also utilize the Kurtosion® feature to make their test profile more realistic. When the software imports files with Random Import, the FDS-generated PSD is Gaussian due to the Henderson-Piersol fatigue damage calculation1. As real-world vibrations are not always Gaussian, the engineer may want to adjust the kurtosis value to match the real-world environment.
A higher kurtosis value will re-introduce the larger peaks that a Gaussian calculation removes, and the test will include more of the high-peak accelerations that are a primary cause of product damage. Consequently, by increasing the kurtosis value, the test will achieve the life dose of fatigue more quickly. It will do so, however, with a lower RMS value.
Summary
According to Miner’s rule, the fatigue a product experiences accumulates. VibrationVIEW’s Random Import option uses this concept to bring a product to failure faster by decreasing test duration. Decreasing test duration increases the RMS level, which accumulates fatigue faster.
Engineers can also use the Random Import option to combine different vibration environments into one test profile. Finally, they can apply kurtosis control (Kurtosion®) to the test profile, further accelerating the test and making it more realistic.
Ready to learn more? Watch a tech talk video or read a case study.