What is a CubeSat?
CubeSats are small satellites built to standard dimensions and launched as auxiliary payloads. They are sent into space with large and expensive equipment, such as a telecommunications satellite, or fit into extra space on a resupply mission to the International Space Station.
Vibration testing instills confidence that the test item will withstand the highest payload and function afterward if needed.
Vibration Testing Systems
Perform shock and random testing with a complete Vibration Research (VR) testing system, including the controller, shaker, and software. The VibrationVIEW supports 104,000 lines of control for low-frequency control and a low noise floor for a greater dynamic range.
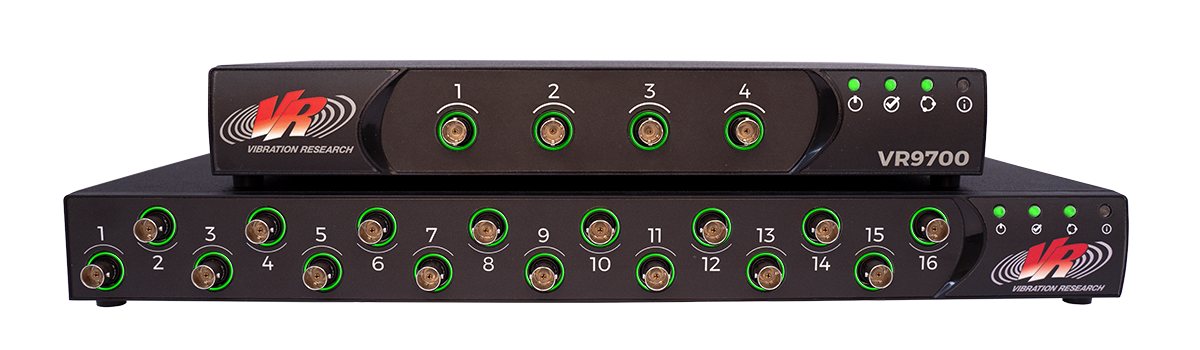
VR9700 I/O Unit
Vibration Research’s high-powered control hardware for vibration and shock testing. Scalable to 128 channels and compatible with all electrodynamic and servo-hydraulic shakers. Features include up to 256 kHz sample rate and 2 outputs.
VR10500 I/O Unit
Vibration Research’s high channel count control hardware for vibration and shock testing. Scalable to 512 channels and compatible with all electrodynamic and servo-hydraulic shakers. Features include up to 256 kHz sample rate and 4 outputs for multiple shakers.
Vibration Control Systems
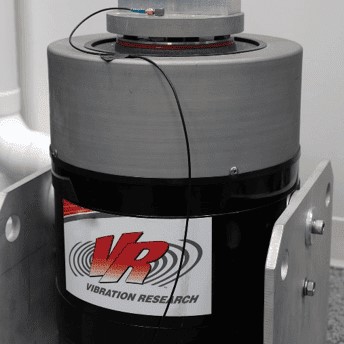
VR control hardware is compatible with all electrodynamic and servo-hydraulic shakers. Its electrodynamic shaker systems consist of a shaker and a matching linear direct-coupled power amplifier.
Additional components may be added to the basic system for a customized system. The systems have been designed and manufactured with shakers and matching amplifiers in tandem.
Multi-Axis Testing
Mount the device under test in the three linear directions or employ multi-axis testing to run all three directions simultaneously. Three-axis testing is accomplished by random vibration testing along each axis using identical or individualized test profiles. The configuration creates a more realistic test compared to traditional single-axis testing.
The VibrationVIEW software allows 2 to 3 test profiles and 2 to 3 control loops to be performed on the x, y, or z-axis.
3-Axis Control
NASA-STD-7001B
Commercially available technology, such as the tested spectrometer, is effective for staying within budget constraints. Space-qualified spectrometers are on the order of $100K each, while off-the-shelf spectrometers cost significantly less.
However, maintaining a budget is meaningless without confidence that the off-the-shelf technology will survive a launch. Vibration testing is required to establish mission viability.
For a spectrometer vibration test, engineers can implement NASA-STD-7001B, a standard that verifies the survivability of spaceflight payload hardware. NASA-STD-7001B is defined for payload testing when the launch vehicle has not yet been determined.
CubeSat Projects with WMU
In 2019 and 2025, Vibration Research engaged with students from Western Michigan University (WMU) to assist with CubeSat Vibration Testing.
- In 2019, the students ran an initial set of tests on an off-the-shelf spectrometer.
- In 2025, the students sought to qualify the main circuit board of their sensor prototype.
Easy & Customizable Setup
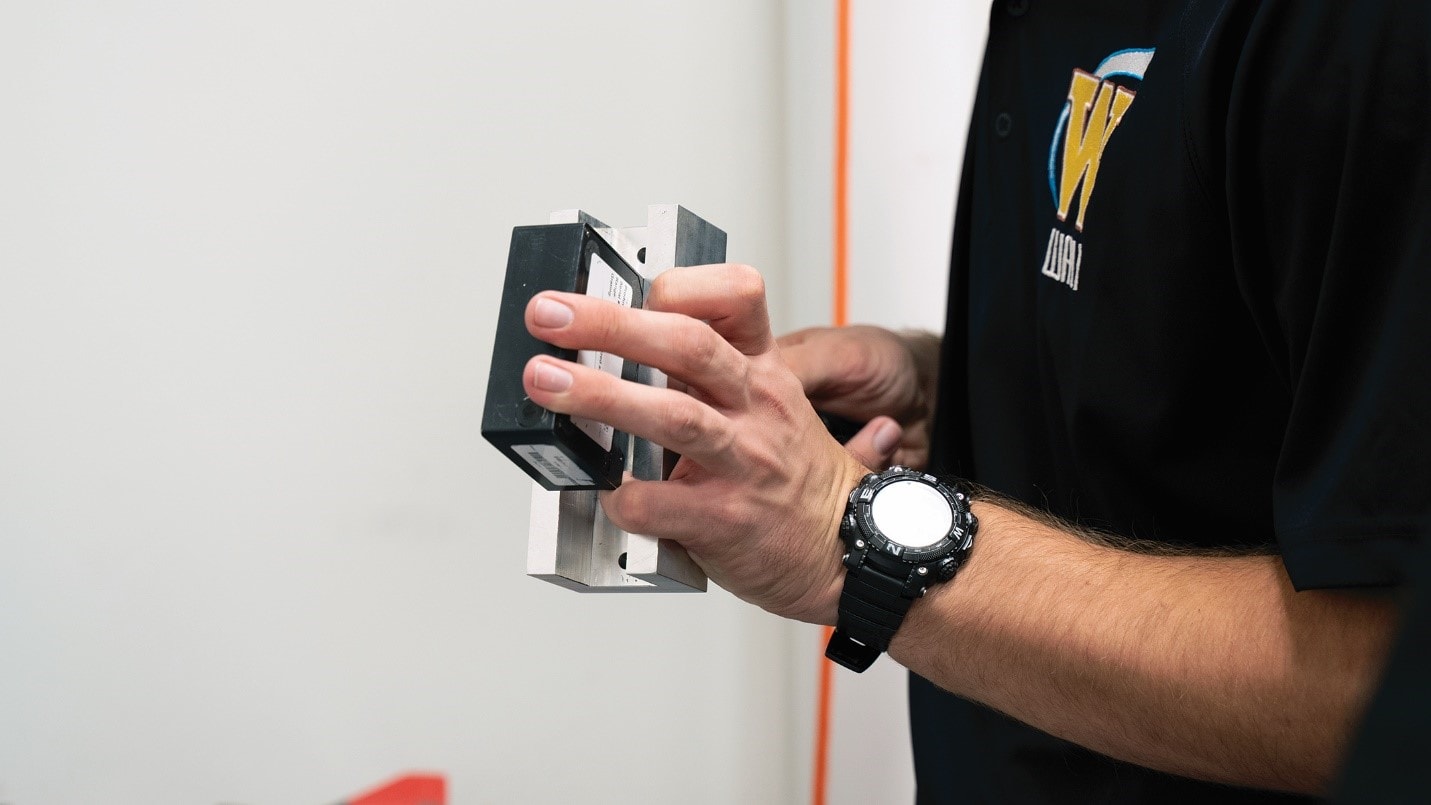
Random Vibration Testing
Perform random vibration testing with standard test specifications or a user-defined test profile.
- Enter frequency/amplitude breakpoints in an easy-to-read, tabular format
- Control constant or ramped acceleration, velocity, or displacement
- Automatically calculate the frequency of intersection between any constant acceleration, velocity, or displacement lines
- Enter over 9,999 separate frequency/amplitude breakpoints to meet virtually any test specification
Short Duration Random Testing
Aerospace facilities often test high-value equipment at extremely high levels of random vibration for a brief period.
Short-duration random vibration tests typically have tight tolerances (±1.5 dB). The statistics of averaging FFT power values limit the possibility that all lines will be within tolerance in a short timeframe. Instant Degrees of Freedom® (iDOF) calculations are a statistically valid way to provide smooth lines and an in-tolerance PSD in a brief testing period.
Fatigue Life Consideration
Use the Fatigue Damage Spectrum software module to create a random test profile that is the damage equivalent to weighted time-history files from the product’s end-use environment.
If You’re Asking These Questions, You Need FDS
- What is the best random test to simulate my product’s environment?
- How long should I be running my random test?
- Can I accelerate my testing?
Sine Resonance Track & Dwell (SRTD) Control
After determining transmissibility peaks, run a dwell test at resonant frequencies for a specified time duration or number of sine wave cycles.
- Manually change SRTD settings while a test is running
- Receive feedback on current test settings in the SRTD Controls
- View long-term changes in the resonance frequency due to fatigue or product temperature
- Customize graph layout of phase-based SRTD graphs
Peak Tracking
Peak tracking in VibrationVIEW automatically shifts resonances by finding and maintaining the peak transmissibility between two channels. It oscillates the phase between the two channels and observes increases or decreases to the peak transmissibility.
This powerful feature minimizes the need for precise detection during the sine sweep so the user can sweep faster. Most importantly, it maintains peak transmissibility throughout the tracked dwell portion of the test.