Notching is a vibration testing control technique engineers can use to limit vibration at an input response channel to prevent over-testing or potential damage.
Article Overview
- Explanation of notching as a method to limit vibration
- How resonances can cause overstress, and why notching is applied
- Different ways to define notches
- Implementation of notching in closed-loop vibration control systems
- Applications across industries
- Use of software tools like VibrationVIEW to configure notches and abort limits
Engineers must account for all responses when running a vibration test. The required test levels may excite the resonant frequency of a component of the device under test (DUT), introducing amplified vibration levels. By applying notching, engineers can control the amplitude at an input channel while meeting the proper test levels.
Notching is particularly useful for DUTs with various bending motions, such as an aircraft wing, critical structures that cannot incur damage, and large DUTs with varying responses.
Notching Applications Across Industries
- Aerospace: Protect critical structures like aircraft wings and fuselages
- Automotive: Prevent damage to components such as engine mounts, suspensions, or electronic modules
- Electronics: Safeguard fragile components like circuit boards and connectors
- Manufacturing: Limit the effects of resonance on large machinery or structural components
- Medical: Prevent over-testing of sensitive devices like implantable sensors or diagnostic tools
- Consumer goods: Protect delicate parts in appliances or high-performance gadgets
How a Notch Works
The International Organization for Standardization defines notching as the “reduction of the input level or spectrum in a vibration testing to limit structural responses at resonant frequencies according to qualification or acceptance loads to avoid over-testing.”1
A notch defines the maximum limit at an input channel. In a vibration control system, an input channel typically measures the DUT’s response via a transducer at a defined location.
The notch value is relative to the test demand. In the VibrationVIEW software, a notch can be a decibel (dB) level above/below the demand or a user-defined table. The limits engineers select may derive from a field recording, previous testing, or a test standard.
Control Process
A vibration test runs on a closed-loop system. The controller sends the drive signal to the power amplifier driving the shaker’s armature. It compares the input response(s) with the demand and adjusts the drive signal, if necessary.
If a response channel includes a notch limit, the system will indicate if the transducer’s measurement deviates from the demand by the defined level. If so, the software reduces (or notches) the drive until the response reaches the correct level. The system does not adjust the drive signal at frequencies where the input response is below the limit.
A notch does not remove frequencies from the spectrum but limits the peak amplitudes in the notched range. If an engineer wants the test to shut down if it exceeds a defined level, they should define an abort limit instead.
In VibrationVIEW, engineers can define a notch for individual measurement channels. They can also define an abort limit simultaneously to individual channels.
Additional Notching Applications
Many industry applications of notching protect the DUT from damage, but notching can serve other purposes, including:
- Ensuring vibration profiles meet industry-specific test specifications without over-exciting certain frequencies
- Preventing excessive vibration of the test fixture, which could compromise test accuracy
- Limiting vibration levels to safeguard transducers from exceeding operational limits
- Minimizing noise or distortion in response measurements due to excessive vibration amplitudes
- Matching real-world vibration environments by attenuating unrealistic resonances
- Reducing unnecessary wear on test equipment, prolonging its lifespan, and optimizing test efficiency
Sine & Random Notching
In VibrationVIEW, a notch can be defined in a sine sweep or random test profile and can limit acceleration, velocity, or displacement measurements.
Sine Testing
A sine sweep test sweeps through a frequency spectrum, outputting a single-frequency sine tone at a defined amplitude and duration. It helps identify resonant frequencies and can expose the test item to a single resonance until failure.
A sine test can excite resonances to high acceleration (G) levels because it runs a fixed-frequency tone. A sine test notch can limit excessive responses at specific resonances while allowing other frequencies to remain at the required test levels.
Random Testing
A random test excites all frequencies in a defined spectrum that might occur at any given time. By exciting all resonances, engineers can determine the interaction between them. Unlike a sine test, which is often controlled at a peak G level, a random test is controlled at a power spectral density (PSD) level.
Notching can target behavior at specific frequency bands where dynamic interactions are known to occur, leading to unrepresentative or damaging response levels. The PSD level is adjusted locally when applying notching, not over the entire spectrum.
WATCH: VibrationVIEW Random Notch video
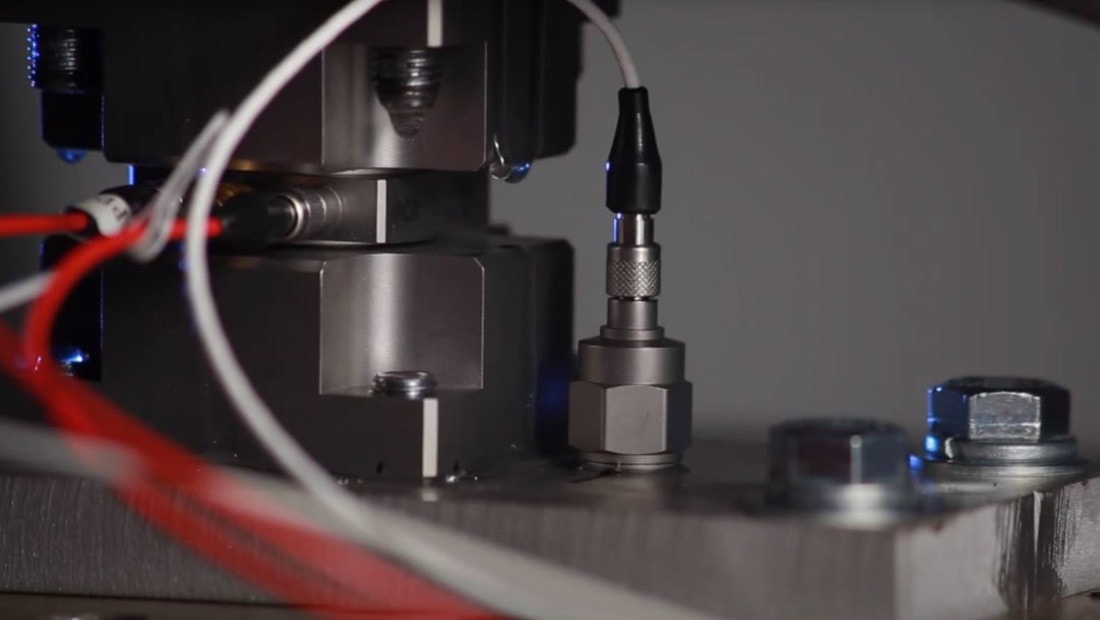
A force transducer mounted to a shaker system.
Force Limiting
An alternate unit, such as force, is also valid for notching if the channel is configured for a force transducer. Force limiting is often implemented in aerospace testing when the mechanical impendence of the shaker may result in over-testing.
Notch at the Response or Control?
A test engineer can set limits on a response channel to account for resonance peaks that may appear during testing. Using notching, the engineer can avoid damaging resonances while testing at others.
Some advocate that notching is unnecessary because the drive compensates for resonance. Although the drive signal compensates for product resonances, it does so across the frequency spectrum. Therefore, it is wise to use notching in appropriate locations to avoid testing around unwanted resonances.
However, as far as control channels are concerned, there is no need to use notching because the drive signal accomplishes the same goal as the notch on the control channel.
Notching in Vibration Testing
Notching is a vibration control technique that engineers can apply to protect sensitive components by limiting the input at specific frequencies. By defining notch limits, they can maintain desired test levels while preventing damage. Implemented in closed-loop systems like VibrationVIEW, notching assists in safe test control across multiple channels and supports compliance with industry standards.