The Sampling & Reconstruction course at Vibration Research University (VRU) introduces the fundamental mathematics of sampling a time-domain waveform. Notably, it discusses the Nyquist rate, which the vibration testing industry uses as a guideline for selecting an appropriate sampling rate, keeping in mind the benefits/risks of under- or over-sampling.
While the Nyquist rate provides a theoretical baseline, real-world applications may require additional considerations. The analysis equipment/tools and device under test factor into the effective sample rate and accuracy of the recorded frequency content. This article explores these practical considerations when determining an optimal sampling rate for field measurements and machine condition monitoring.
Determining Frequency Requirements
To determine the Nyquist rate, you must know the highest frequency of interest. However, faults at high frequencies may not be apparent in the overall signal or relevant to your test objectives. The following are several considerations when determining the frequency range of interest for sample rate selection.
Vibration Signal Behavior
Understanding the signal behavior of the recording environment helps engineers select a sample rate that captures meaningful data without oversampling unnecessarily.
Behavior Type | Description | Sampling Need |
Steady-State | Continuous, periodic or constant signals | Moderate (depends on maximum frequency) |
Transient | Short-duration, impulsive events | High (captures sharp edges) |
Random | Non-periodic, broadband | Depends on specified bandwidth |
Steady-state
Steady-state vibration involves continuous, periodic signals, such as imbalance, misalignment, or harmonics. The frequency content is narrow and stable. A lower sample rate may be sufficient so long as it accounts for the highest frequency of interest.
Structural vibration is typically steady-state and low frequency and originates from modal behavior or resonances in a stationary system. Rotational vibration, driven by dynamic machine components, can exhibit steady and transient behaviors over a wider frequency range.
Transient
Transient vibration involves short-duration, high-frequency events such as impacts, faults, or switching. Recording these events requires a high sample rate to capture the narrow time window and wide frequency bandwidth. Under-sampling can omit the event or distort its shape or frequency.
Random
Random vibration involves non-periodic broadband excitation and is common in environmental testing where vibration profiles are defined statistically, such as aerospace qualification. The frequency range of interest largely depends on the test specification/objective, as random excitation can occur at any range of frequencies depending on the DUT.
Sampling rates must also meet relevant standards or test specifications, which often define required bandwidths regardless of the DUT’s response.
Additional Considerations
Resonant Frequencies
System resonances amplify the signal response at specific frequencies, which can distort the signal. The sample rate and filter setup should exclude or properly capture resonances, if necessary.
Fault Frequency
High-frequency faults such as bearing defects or gear mesh may occur above the dominant vibration energy. The sample rate should be fast enough to capture and isolate these signals.
Hardware Constraints on (or Support of) Sample Rate
After calculating the Nyquist rate and determining an ideal sampling rate, engineers must confirm that their equipment can support this value.
Sensor Bandwidth and Resonant Frequency
Sensor bandwidth and resonant frequency help define the upper limit for a sample rate. A sensor’s bandwidth determines the range of frequencies it can accurately measure and output without significant distortion or loss. The usable bandwidth ends well before the sensor’s resonant frequency to avoid distortion.
Analog-to-digital Conversion (ADC) Limitations
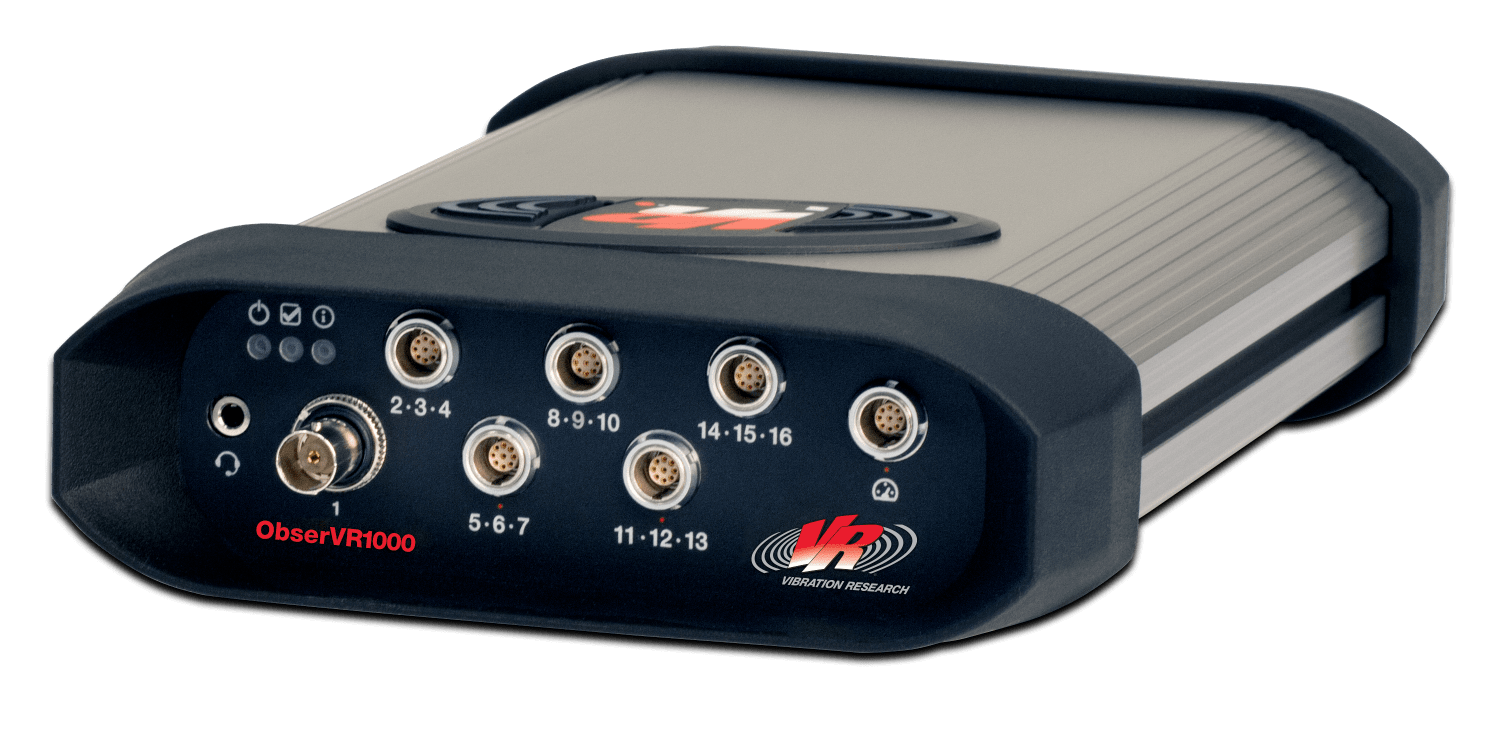
The ObserVR1000 data acquisition system has a 24-bit ADC.
The ADC capabilities of the data acquisition system determine the limitations and precision of the time waveform recording. For example, the maximum sampling rate sets the upper limit for how fast the ADC can digitize analog input.
The bit resolution affects amplitude precision and dynamic range. A higher bit depth improves the system’s ability to detect small faults in the presence of dominant signals or background noise.
Anti-aliasing Filters and Cutoff Behavior
Aliasing is a signal distortion that occurs when sampling below the Nyquist rate. Many data acquisition (DAQ) hardware devices have built-in analog low-pass filters fixed or tied to the sample rate that block a specific range of high-frequency content. Anti-aliasing filters are a necessary constraint: they protect data quality but limit the maximum measurement regardless of sample rate.
Your highest frequency of interest must be below the filter cutoff to avoid attenuation. The industry standard is to select a sample rate 2.5 to 3 times higher than the highest frequency of interest to allow for filter roll-off.
Time Resolution vs. Frequency Content
You should consider time resolution and frequency content when selecting a sample rate. Many vibration test engineers focus on the frequency content because industry-standard analyses are in the frequency domain (FFT, PSD, etc.), and many standards define vibration levels in frequency.
However, time-domain analysis may be necessary for capturing transient or shock events, time waveform statistics, or non-repetitive, time-dependent faults.
Frequency Content
Sets the minimum sample rate to avoid aliasing
Time Resolution
Determines how precisely to capture event timing or shape
An engineer may sample fast enough for frequency but miss time-domain features like peak amplitude or event duration.
Time-Based Fault Detection
Time-domain analysis may be necessary when faults are non-repetitive or short-duration. Faults that are time-dependent typically involve transients, non-periodic events, or faults whose critical indicators appear in a time waveform rather than the frequency spectrum.
The following fault types may appear as a function of time:
- Impacts or transients
- Early stage bearing defects
- Loose mechanical fitments
- Misfire or combustion events
- One-time fault events
Post-process Considerations
More than just the frequency bandwidth, the sampling rate affects how well data can be filtered, analyzed, and interpreted after recording.
Spectral Resolution
A higher sample rate increases the frequency range but captures fewer samples per frequency bin unless the recording time is increased. This tradeoff can make it harder to resolve narrowband features in the frequency domain unless a sufficient signal duration is captured.
Noise & Signal Quality
Oversampling can improve post-processing. It reduces quantization noise and allows for more effective filtering or signal averaging, which may be beneficial in noisy environments.