This month, Vibration Research offered its expertise and equipment to support a CubeSat project of Western Michigan University (WMU) students. The overall goal of the project is to design and test a payload that will be launched onboard a NearSpace Launch Thin-Sat™. Vibration Research assisted in performing an initial qualification test of the payload’s main circuit board.
CubeSat Qualification Tests
Engineers perform qualification tests on the components and subsystems of CubeSats and other small satellite projects to ensure that the prototype can endure the launch and space environments. Typically, the engineer defines the pass/fail criteria prior to the test and evaluates the function of the prototype after. Engineers often perform these tests at the early stages of development when they are identifying and addressing issues with components before full system testing.
The Goddard Space Flight Center recommends full-system verification testing but recognizes the need for testing lower levels of assembly1. Full environmental verification with realistic test levels is necessary to ensure a system will survive a flight.
Project Details
The Thin-Sat is a CubeSat roughly 4 x 4 x 2 in. The WMU students plan to include a prototype for an electric propulsion sensor in the launch. The maximum dimensions of the assembly are 91 x 95 x 41 mm, and it includes four 2-56 UNC threaded standoffs on the bottom which serve as the mount to the rest of the satellite.
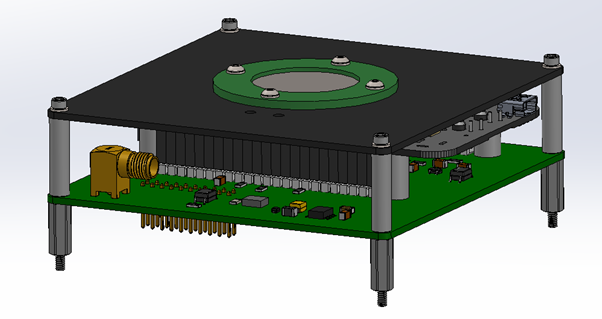
CAD of the prototype.
The WMU students sought to qualify the main circuit board of their sensor prototype. First, they performed a random vibration test on one prototype at Vibration Research. After the test, they evaluated the electrical performance. Any change in performance that would prevent the prototype’s function is considered a failure. If the prototype passes, then they will send multiple of the prototype to NearSpace for additional qualification testing on a larger shaker.
GEVS Random Vibration Test
NearSpace advised the students to run a random vibration test as outlined in the General Environmental Verification Standard (GEVS), which is a NASA standard. The students used GSFC-STD-7000B: Generalized Random Vibration Test Levels Components (ELV), 22.7-kg (50-lb) or less based on their prototype. Table 1 provides the test levels from Table 2.4-3 in GSFC-STD-7000B (property of Goddard Space Flight Center).
Frequency (Hz) | ASD Level (/Hz) |
20 | 0.026 |
20-50 | +6 dB/oct |
50-800 | 0.16 |
800-2000 | -6 dB/oct |
2000 | 0.026 |
Overall: 14.1 GRMS
The standard requires the test facility to use properly calibrated equipment, and a single-axis accelerometer was used for control. The test was run for 90 seconds.
Next Steps
After testing, the students qualified their prototype and moved forward with additional testing. Vibration Research wishes them the best of luck with their launch!