Highly accelerated life testing (HALT) is a well-established test-to-failure technique engineers use to identify product weaknesses. HALT requires a pneumatically actuated repetitive shock vibration table in a liquid nitrogen (LN2) thermal chamber. These systems can be costly, and purchasing one is not practical for many test labs.
Vibration Research has introduced the rapid failure mode precipitation testing (RFMPT™) technique as an alternative to HALT. RFMPT does not require special test equipment and offers several benefits over traditional HALT. While RFMPT is like HALT in many respects, it also provides insight into the likelihood of failure when a product is in the customer’s possession. It also takes advantage of equipment available in most test labs. Let’s look at the similarities and differences between HALT and RFMPT.
Equipment
A HALT chamber consists of a vibration table actuated by pneumatic repetitive shock hammers strategically positioned under the table at various angles. Accordingly, the hammers input energy into the system at multiple degrees of freedom without accurately or repeatedly regulating the frequency and amplitude content in the axes of interest or across the table surface. The repetitive shock actuators provide vibration that stimulates but does not simulate.
A typical HALT setup also includes an enclosure with heaters and LN2 dispensers for rapid thermal transitions and offers add-on features for humidity cycling or other environmental stressors. HALT chambers are best suited for low-mass products, particularly those with circuit card assemblies using small form factors.
Due to the size constraints of a HALT chamber, the relatively low payload capability of the pneumatic hammers, and the environmental variability over the surface of the HALT table, HALT can only test a limited number of samples at once. These constraints also limit the fixturing setup to arrangements that do not typically reflect boundary conditions in the product’s service environment. RFMPT setups have more flexibility, better repeatability, more payload capacity and, as a result, are not as constrained in their application.
Excitation
The pneumatically actuated hammers underneath the HALT table generate repetitive excitations. The resulting vibration is random-like, but the repeated burst stimulation leads to higher, unmoderated kurtosis values than in the field or on a typical electrodynamic shaker. While engineers can control the overall multiaxial gRMS as a single resultant value, the intensity can vary extensively between axes (x, y, z) and table location, leading to inconsistent part-to-part and test-to-test results.
RFMPT, on the other hand, can be performed on a traditional electrodynamic shaker table or a hydraulically or servo-electrically actuated shaker table. Special testing equipment is not necessary; engineers can adapt what they have on hand. Thus, they can control the frequency content and amplitude distribution using various multi-point control schemes. The addition of Vibration Research’s patented Kurtosion® control appropriately inputs field-representative kurtosis levels into the test articles. This quality of RFMPT leads to consistent part-to-part and test-to-test repeatability and the potential of correlation to measured field data and service life fatigue.
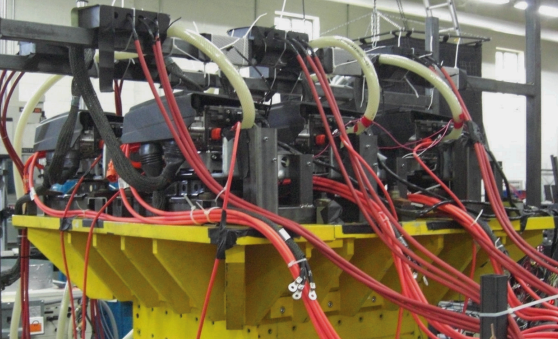
RFMPT setup for a power inverter.
Stressors
The HALT methodology employs a step-stress approach. The chamber applies accelerated stresses to the DUT, incrementally increasing the stress levels while sustaining them for a uniform time between each step. HALT often combines multiple stressors in addition to vibration, such as temperature, humidity, and mechanical/electrical cycling, simultaneously or back-to-back.
HALT can perform rapid thermal transitions to accelerate fatigue damage. A typical HALT chamber is inherently capable of rapid thermal transitions using high-powered heaters and LN2. An RFMPT setup can also achieve rapid thermal transitions in a conventional thermal chamber that encloses the shaker table if adequate external capability is available.
Rapid thermal transitions can help with test acceleration, but their usefulness relies on the system’s ability to transition temperature on the test parts, not just the surrounding air. This temperature transition becomes more challenging for large test articles.
Like HALT, RFMPT is a step-stress methodology and a test-to-failure. The difference, however, is that each step in the RFMPT process has a known relationship to stresses in the field. Consequently, engineers can correlate failures to service life and avoid so-called “foolish failures” upfront.
Identifying Operation and Destruct Limits
An operational limit is the stress necessary to cause a recoverable malfunction, whereas a destruct limit is the stress necessary to cause a permanent or “hard” failure. Both the HALT and RFMPT processes determine the operation and destruction limits. This information provides a benchmark engineers can compare with safety/performance/reliability requirements as specified in a product’s controlling technical design documents. It also allows for A/B comparisons with iterations of the product design and against competitors’ designs.
Unlike HALT, RFMPT helps explain test acceleration factors when correlating testing, reliability growth, and overall robustness to end-use environments.
Application
HALT is an accelerated test type. In the interest of achieving failures quickly, it typically employs stress levels that exceed what engineers expect in the operational environment. HALT tests cannot be directly correlated to measured (or analytically anticipated) service life because HALT test control is limited to a gross single-point gRMS value to represent all degrees of freedom everywhere on the test table, and frequency versus amplitude is uncontrollable. This is a significant limitation of HALT. RFMPT, with its inherently tighter control of frequency and amplitude, naturally overcomes this limitation.
Additionally, engineers can use Vibration Research FDS and SRS analyses to ensure their test levels are relevant to the end-use environment and avoid “foolish failures” upfront. They can use both HALT and RFMPT for A/B comparisons, but only RFMPT can relate failures to customer usage and correlate boundary conditions for digital twins.
HALT and RFMPT can take up to a month to complete, depending on the complexity of the test setup and the rounds of test-break-repair-test cycles needed. HALT is most beneficial in the very early stages of the product development cycle. It can quickly break small parts to uncover design weaknesses, both actual and potentially foolish, thereby incorporating design changes when the cost to implement them is minimal, and the opportunity to build robustness is high, particularly for electronic circuit card assemblies. RFMPT, on the other hand, is an adaptable and more comprehensive test method that engineers can use throughout the product development cycle.
Conclusion
HALT and RFMPT are accelerated step stress tests-to-failure focused primarily on vibration and thermally induced failures. Both methods are adaptable to other environmental stressors, including humidity and electrical/mechanical cycling. The most significant differentiators between the two methods:
- RFMPT’s flexibility to use standard and readily available test equipment
- RFMPT’s superior control of vibration inputs
- RFMPT’s part-to-part and test-to-test consistency
- RFMPT’s direct correlation to customer usage
To learn more about RFMPT, please watch our video on the topic. Please also refer to the companion article on RFMPT, “Test to Failure with RFMPT.”